Welding is a common practice in many industries, but it can be dangerous if not done correctly. In this blog post, we’ll go over some tips for welding safety. We’ll also discuss the importance of wearing the proper safety gear and taking other precautions to avoid injury.
What is welding?
Welding is a process of joining two materials together using heat and pressure. The most common type of welding is metal welding, but there are other types of welding as well, such as plastic welding and glass welding. But today we are going to focus on metal welding.
There are a few different ways to weld, but the most common method is arc welding. This type of welding uses an electric arc to create heat, which melts the metals being joined together. As the metals cool, they form a bond.
There is also MIG welding which stands for ‘Metal Inert Gas’ welding. This type of welding uses a wire that is fed through a welding gun, which melts the metal and creates a bond between the two pieces.
TIG welding, or ‘Tungsten Inert Gas’ welding, is similar to MIG welding but instead of using a wire, a tungsten electrode is used to create the arc. This type of welding is often used for thin metals and for projects that require precision.
There is also resistance welding, which uses electricity to create heat and pressure to weld the metals together. This type of welding is often used for projects that require a strong bond, such as cars and airplanes.
What tasks require welding?
There are many types of tasks in the workplace that may require welding, even if it isn’t the main business. For example, a construction company may need to weld two pieces of metal together during the building process. An automotive shop may need to weld a broken car part back together. A manufacturing company may use welding to create products from scratch.
The type of welding required for each task will vary depending on the materials being used and the desired outcome. It’s important to select the appropriate welding method and have the necessary training before attempting any welding tasks. Ensure you hire the right person for the job, and don’t take short cuts just to get something done quickly.
Why is welding dangerous?
Welding can be dangerous if not done properly, with the correct training and control measures. The most common risks associated with welding are burns, eye damage, fume inhalation and electric shock.
When welding a person can be exposed to temperatures of between 3000 and 20 000 degrees Celsius. That is hot enough to cause 3rd degree burns. Welding also produces harmful fumes and gases that can be damaging to a person’s health if inhaled. These fumes can contain metals and chemicals that can lead to lung disease or other health problems.
Another hazard associated with welding is electric shock. This can happen if the welder comes into contact with an electrical current. Electric shock can cause burns, muscle spasms and even death.
However by ensuring welding safety, these risks can be significantly reduced.
Let’s get into the specifics.
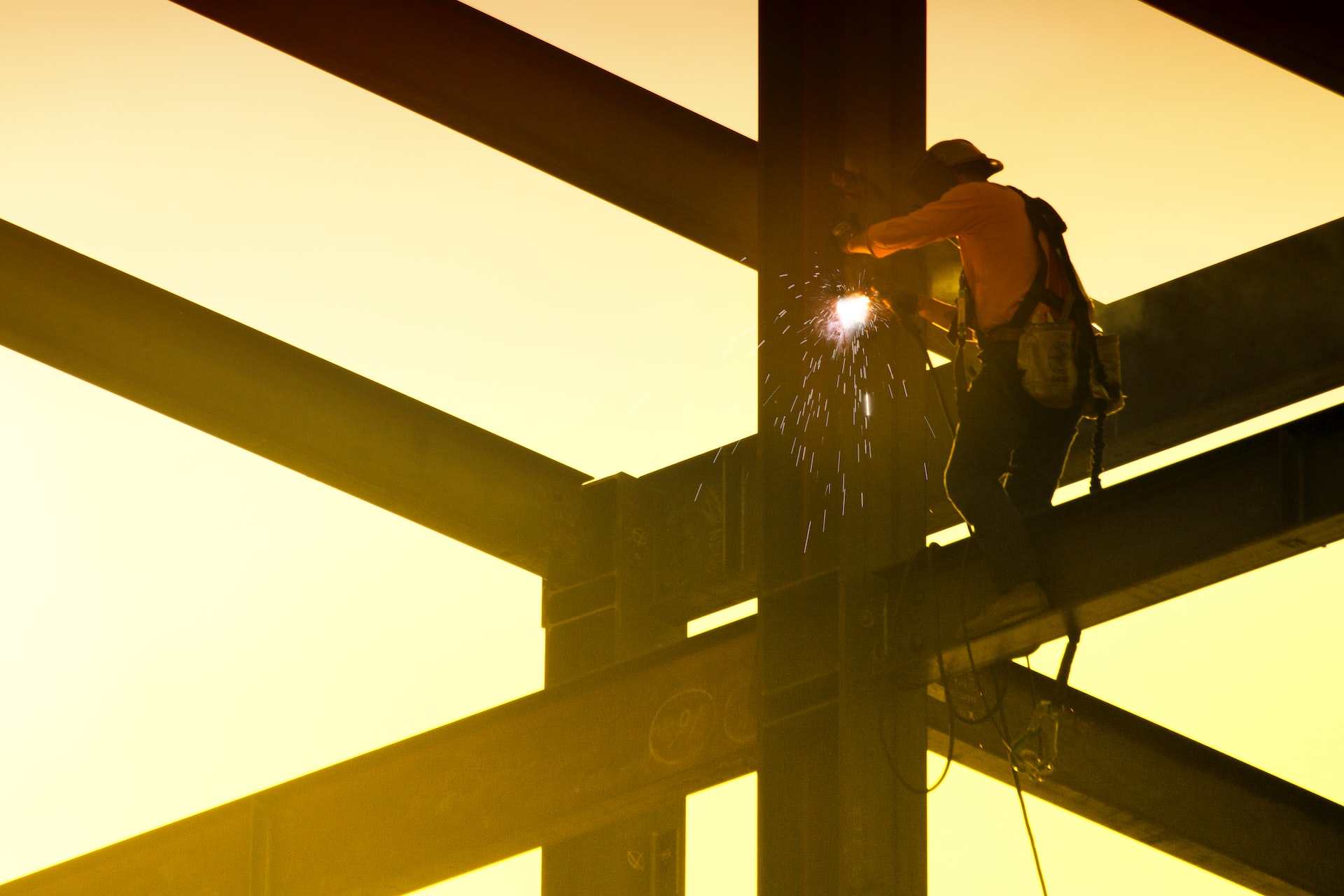
What are the hazards and risks associated with welding?
Airborne
Fumes, mists, dust, vapours, and gases, such as ozone, can be created while welding. The procedure and the materials used, such as metals, solvents, flux, paint, and polymers, determine how much and what kind of fumes are produced. Welding fumes are made up of tiny particles of metal, including lead, cadmium, nickel, and chromium. These metals can damage your lungs, brain, and other organs.Fumes, dust, vapour, and gases can harm your health in a variety of ways.
Asphyxiation, asthma, wheezing, metal fume fever, lung damage, bronchitis, cancer, pneumonia, and emphysema are just a few of the possible side effects. Other effects include nose and throat discomfort.
Some welding fumes are visible right away. On the other hand, many vapours, mists, dust, vapours, and gases cannot be seen. When compared to electric welding, gas welding often produces less pollutants.
The effects of welding fumes depend on the amount of exposure and how often you are exposed. However, all welders should take proper precautions to protect themselves.
There are two ways that welding fumes can enter your body: through your lungs or through your skin. The most common way is by breathing them in.
Radiation
Radiation is energy that moves through space as subatomic particles or as waves of electromagnetic radiation.
When laser welding and electric arc welding are performed, UV, visible light, and infrared radiation are created. Gas welding makes both infrared light and visible light.
How radiation might affect your body depends on its type, how strong it is, how close you are to it, and how long you are around it. Getting a lot of ultraviolet and infrared radiation while welding can cause eye problems and burns. Arc eye, also called “welder’s flash,” is a severe irritation of the cornea caused by too much light. The cornea only needs one or two days to heal, however, if you do not treat it right away, arc eye can lead to more serious problems such as ulcers.
Laser welding produces a very intense and focused beam of light. As a result, this type of welding can cause severe burns in a very short amount of time.
You might also be exposed to ionizing radiation while welding. This is a type of radiation that can cause damage to your cells and DNA. It has been linked to cancer.
Ionizing radiation is produced during electric arc welding, laser-beam welding, and plasma-arc welding. The amount of ionizing radiation you are exposed to during these processes depends on the length of time you are welding and how close you are to the welding area
You can be exposed to non-ionizing radiation while welding, too. This type of radiation does not cause damage to your cells or DNA but can still be harmful. For example, it has been linked to cataracts. Non-ionizing radiation is produced during gas welding, electric arc welding, and laser-beam welding.
Most of the time, it takes time for the effects of UV and infrared radiation to show up. Even though the radiation from laser welding isn’t as clear as the radiation from electric welding flames, both are very dangerous.
The people who are doing the welding are the ones who are most likely to get hurt. But people who walk by or work in the area could also be affected by radiation exposure.
Electric Shock
As with any task that uses a piece of equipment or tool that uses electricity, welding poses a risk of electric shock. When you are welding, you are working with high-voltage electricity. This means that if you are not careful, you could get an electric shock.
Electric shock happens when the electrical current from the welding machine goes through your body. It can cause burns, muscle spasms, and even heart problems. In severe cases, it can be deadly.
Electromagnetic Fields
Using a welder can expose you to very strong electromagnetic fields, also known as EMFs. These fields are made up of electricity and magnetism. They are found in everything from power lines to microwaves to X-rays.
EMFs have been linked to cancer, so it is important to take precautions when working with them. They also pose a risk of harm to those who have pacemakers or other electronic devices in their bodies. So it is important that anyone in the vicinity is aware of the EMF exposure and takes precautions accordingly.
Noise
Welding can be very loud. In fact, the noise level from some welders can be as loud as a jet engine. Prolonged exposure to this noise can cause noise induced hearing loss and other noise induced injuries such as tinnitus.
Fire and explosions
The sparks created by welding can also cause fires, in fact a major bushfire in New South Wales in December 2019 was started by fencing contractors welding. In another incident, an abattoir in South Australia was destroyed in 2018 when a maintenance worker was welding without the appropriate controls in place.
Sparks from welding can also cause explosions if they land in the wrong place, which can easily happen in a workplace with many flammable materials in the near vicinity. Some common flammable materials in the workplace include:
- wood
- plastic
- paper
- paint
- solvents
- gases
- oils
And don’t forget, even neighbouring workplaces may have flammable materials that will ignite if a welder’s spark hits it, so always be aware of your surroundings.
Burns and heat exposure
As many welders, and family members of welders can attest, welders seem to always be covered in small burns, called “flash burns”. These happen when the welder’s arc is not completely under their control and a bit of the intense heat and light hits their skin. While these burns are usually not serious, they can be very painful.
More serious burns can occur if the welder is not wearing the proper clothing or safety gear. Welders need to wear clothing that protects them from the intense heat and light. This usually means long-sleeved shirts and pants made from natural fibers such as cotton.
Welding is also very hot work, which is often hard on the welder’s body. In hot weather, or if the welder is working in a confined space, the heat from welding can cause heat exhaustion or heat stroke. These conditions can be very serious and even life-threatening, so it is important to take breaks often, stay hydrated, and wear appropriate clothing.
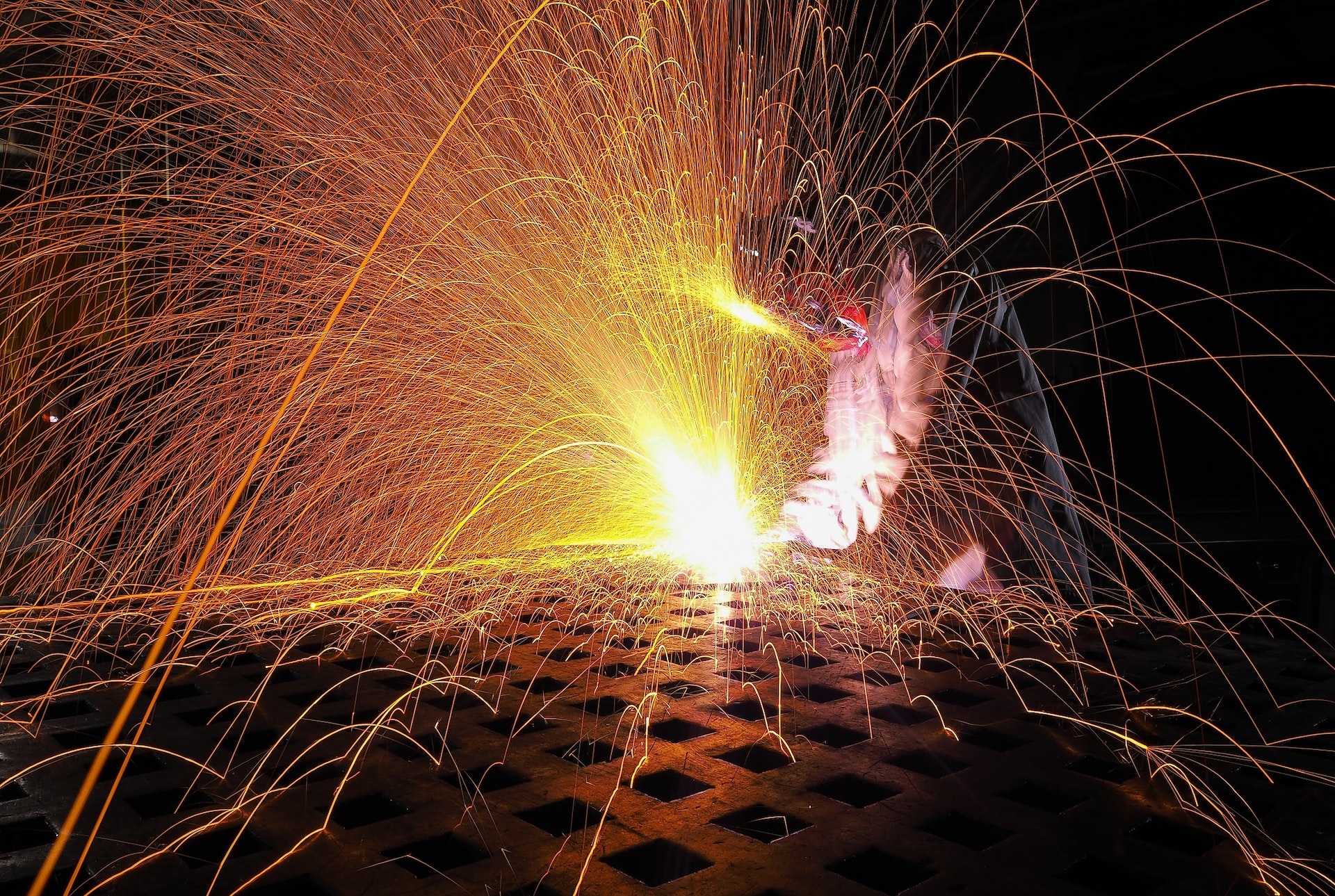
Lead exposure
When welding , lead can be released into the air. Lead is a metal that can be very harmful to people’s health, especially children and pregnant women. Lead exposure can cause problems with the brain, kidneys, and reproductive system. It can also cause high blood pressure and anemia.
Welders may be exposed to lead when welding lead-based metals, such as lead alloys or lead-coated metals. They may also be exposed to lead when welding other metals that contain small amounts of lead, such as copper and brass.
Confined spaces
Sometimes due to the nature of the work, welders may have to work in confined spaces which pose their own risks. Confined spaces are often not well ventilated, so the welder may be exposed to harmful fumes. They may also be at risk of being overcome by heat, noise, or lack of oxygen.
Working in a confined space can also be dangerous because if something goes wrong, it may be difficult for the welder to get out or for others to get to them.
Falls
Welders are also often called upon to work at height , which can pose a risk of fall if the proper safety precautions are not taken. Added to the risk of falls is that they are using heavy and dangerous equipment, which can cause serious injury if it falls on someone. They are often also using a lot of PPE which can make movement and balance more difficult.
Manual handling
Welders are often required to move heavy equipment and materials, which can lead to injuries if not done properly. Manual handling injuries are some of the most common workplace injuries, so it is important that welders know how to lift and carry things safely.
Welding is often a repetitive task, which can lead to repetitive strain injuries such as carpal tunnel syndrome. They may also be required to complete the work in unnatural positions , which can cause musculoskeletal injuries.
Lack of training
Welding is a highly skilled trade and welders need to have the proper training to do the job safely. Unfortunately, not all welders have had the opportunity to receive formal training. This can lead to them being unaware of the risks involved in welding and how to stay safe while doing it. Lack of training can lead to incidents and injuries occurring that not only harm the worker but also those around them.
How to improve welding safety?
As you can see, there is a lot of things that can go wrong while welding. But don’t let that discourage you, because welding is an amazing trade with a lot of opportunity. As long as you implement the correct control measures by following the hierarchy of control you will be able to significantly reduce the risk to yourself, employees and anyone else in the vicinity.
Let’s look at how you can manage all the above risks.
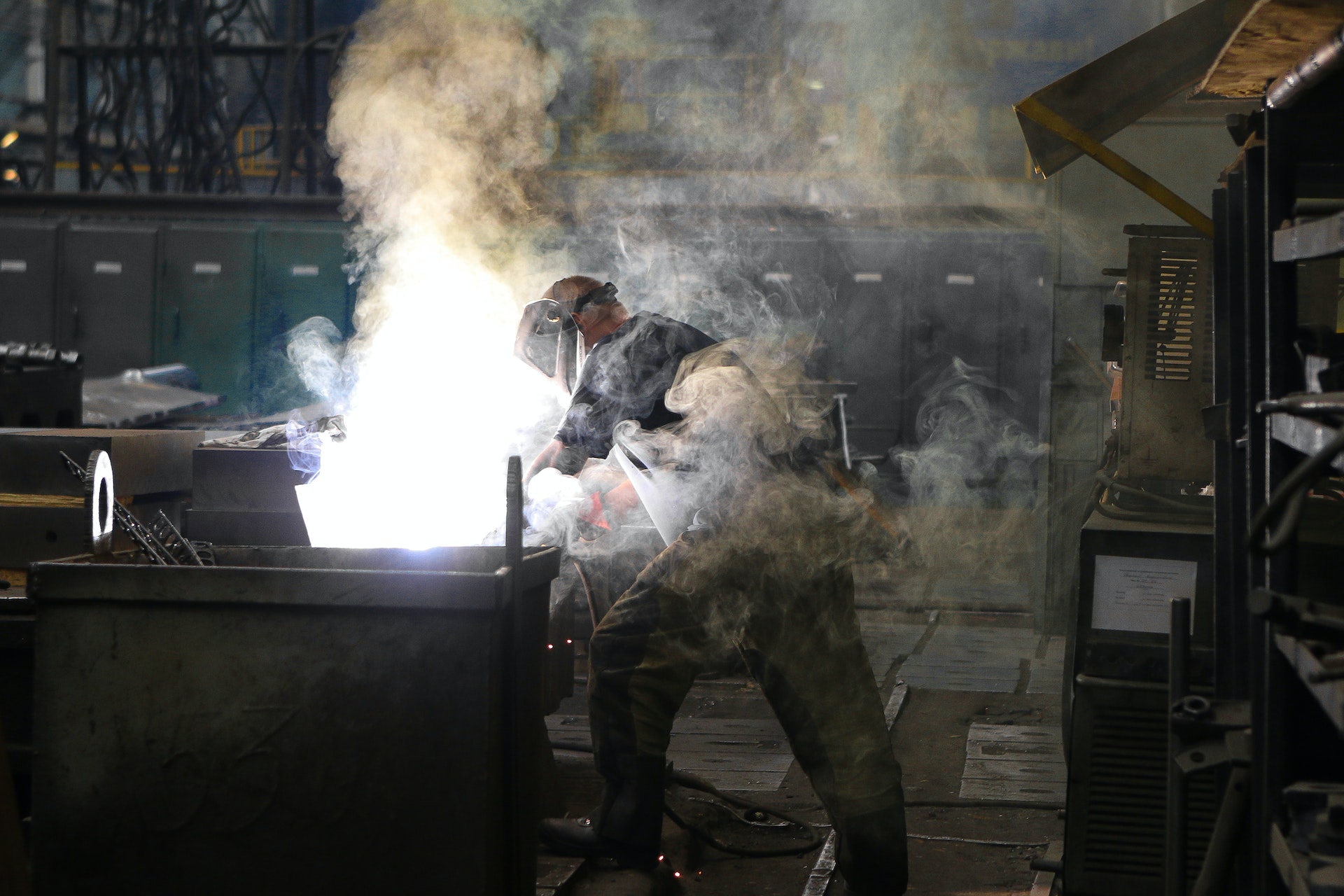
Welding control measures
Because there are so many hazards and risks associated with welding, we are going to make it simple by going through the hierarchy of control and identifying how we can reduce those hazards and risks to improve welding safety.
Elimination controls for welding
The best way to control a hazard is to eliminate it altogether. This is not always possible, but when it is you should do it. If you can weld something without using lead, then don’t use lead. If there is a job that can be done without welding at height, then don’t do it at height. If you can not weld at all, and use a pre-constructed object, then you can eliminate the entire task of welding. Of course, this may introduce different risks, but with a risk assessment you can decide which is the better option to take.
Substitution controls for welding
If you can not eliminate the hazard, then look at substitution. Substitution when welding might be more difficult to do because you are substituting the entire process. However, it is possible to substitute certain materials. For example, you might use a different metal that does not contain lead, or you could use a different welding process that does not produce as many fumes or heat. Technology, equipment and materials are ever evolving , so there might be new options available to you that weren’t before.
Isolation controls for welding
When you can not eliminate or substitute the hazard, you will need to look at isolating it. This means that you put physical barriers or distance between the hazard and people. When welding this might include using screens to protect people from the arc or specific areas that are only for welding to protect people from noise and fumes. It might also mean that you keep people a certain distance away from the work area, or that you only allow certain people in the area when welding is happening.
Engineering controls for welding
Engineering controls should always be used in conjunction with other control measures. When you can not eliminate, substitute or isolate the hazard, you need to look at how you can change the equipment or process to make it safer. This might mean that you use ventilation to remove the fumes, or that you use a water cooler to keep the area cool. It might also mean that you change the way that you are welding to make it easier on your body, or that you use an automated system.
Administrative controls for welding
Administrative controls should be used in conjunction with other control measures as they rely on people understanding and following the procedures. When you can not eliminate, substitute, isolate or change the equipment or process, you need to look at how you can change the way people work. This might mean that you have specific training requirements, or that you have a permit to work system in place. Administrative controls also include things like work procedures, policies, rules and regulations.
Personal protective equipment for welding
Personal protective equipment (PPE) should always be used as a last resort. This is because PPE can fail, it is often uncomfortable to wear and it does not address the root cause of the hazard. When you can not eliminate, substitute, isolate, change the equipment or process, or change the way people work, you will need to provide PPE. This might include things like welding gloves, aprons, helmets, face shields and respirators
When using PPE it is important that you:
- Select the right PPE for the job
- Make sure that the PPE fits properly
- Train employees on how to use the PPE
- Inspect the PPE regularly
- Maintain the PPE
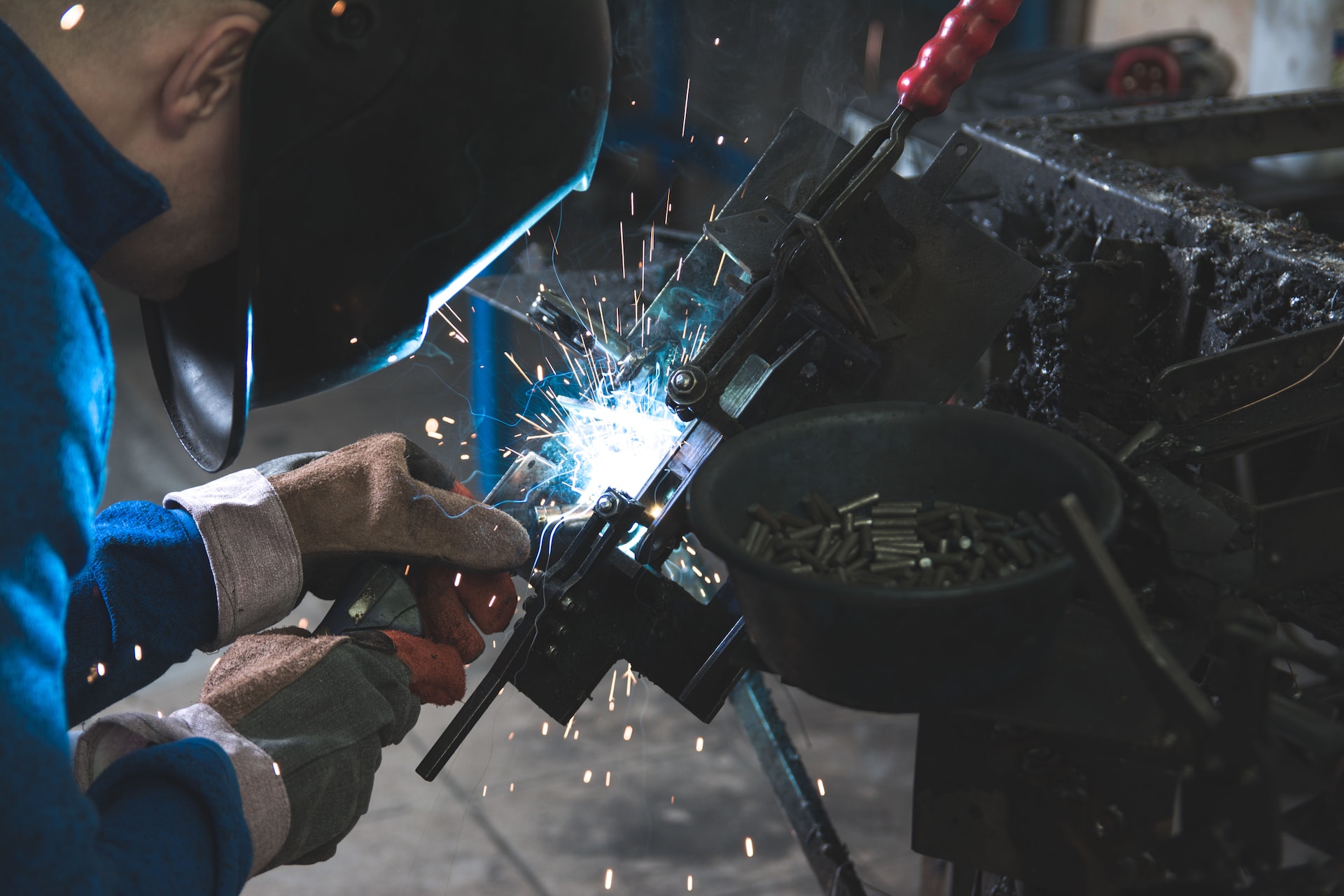
General welding safety tips
- Read the welding safety datasheet for the materials you are using
- Use the right PPE for the job
- Know where the fire extinguisher is located and how to use it
- Keep your work area clean and tidy
- Weld in well-ventilated areas
- Do not weld near flammable materials
- Disconnect hoses when not in use
- Never leave a welding machine unattended
- Use a ground clamp on all metalwork
- Inspect your equipment regularly
- Be aware of your surroundings
- Do not weld in wet or humid conditions
- Wear comfortable clothing
- Do not wear loose clothing or jewelry
- Ensure you are properly trained for the task at hand
- Follow the manufacturer’s instructions
- Take regular breaks
- Ensure you don’t work in the same position for too long
- Use a welding screen or curtains to protect other people in the area
- Never look directly at the arc
- Do not touch hot metalwork
- Do not weld on containers that hold flammable liquids or gases
- Ensure that hoses are not damaged
- Keep abreast of any changes in welding safety regulations and best practices
How to keep safe if someone is welding in your workplace?
If someone is welding in your workplace there are some things you can do to help keep yourself, the welder and others safe. They include:
- Making sure the welder is aware of your presence
- If there are barriers erected, stay out of the welding area
- Wearing the right PPE if you need to go into the welding area
- Being aware of where the fire extinguisher is located
- Knowing how to use the fire extinguisher
- Informing the welder if you see anything that could be unsafe
- Reporting any concerns you have about the welding work to a supervisor
- Don’t look at the welding arc
- Don’t touch hot metalwork or any of the welding equipment
- Don’t leave flammable materials near the welding area
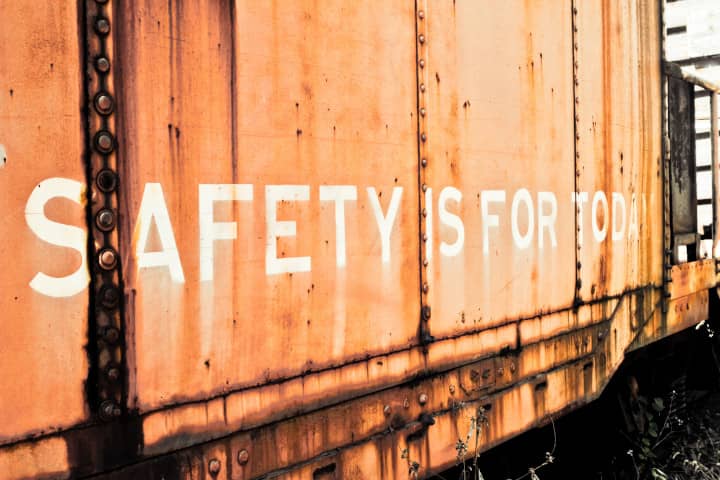
Do I need a safe work method statement for welding?
A safe work method statement is only required for high risk construction work . However, it is good practice to have some sort of written procedure or safe operating procedure for any task that has the potential to cause harm. This should be specific to the task and detail how you will control the hazards associated with welding. By having this in place it provides your workers with the information they need to work safely and it also demonstrates that you have considered the risks involved with the task and taken steps to control them. If an incident occurs, you can use this evidence to show that you have done everything you can to prevent it from happening.
Welding toolbox talks
Toolbox talks should be used to supplement the safety procedures and training that you provide to your employees. A toolbox talk is a short safety meeting that is conducted at the work site on a regular basis. The purpose of a toolbox talk is to raise awareness of hazards and risks, and to reinforce the importance of following safe work practices.
Some things that you might cover in a welding safety toolbox talk include:
- Hazards associated with welding
- The importance of using the right PPE
- How to safely set up and use welding equipment
- The importance of following safe work procedures
- The importance of maintaining equipment
- The dangers of welding in confined spaces
- What to do if you are exposed to fumes or smoke
- The importance of regular breaks
- The dangers of working in wet or humid conditions
- How to safely store welding equipment
When conducting a toolbox talk, you should:
- Make it interactive – ask questions and encourage employees to share their own experiences
- Keep it short – aim for 10-15 minutes
- Make it relevant – focus on topics that are relevant to the work that is being undertaken
- Make sure everyone understands – use plain language and avoid technical jargon
- Encourage questions and feedback – this will help to ensure that employees are engaged and understand the content of the talk.
Welding safety resources
There are a number of welding safety resources available that can be used to supplement your safety procedures and training. Some of these resources include:
Welding safety checklist
This checklist can be used to assess the safety hazards associated with welding, and to ensure that appropriate control measures are in place.
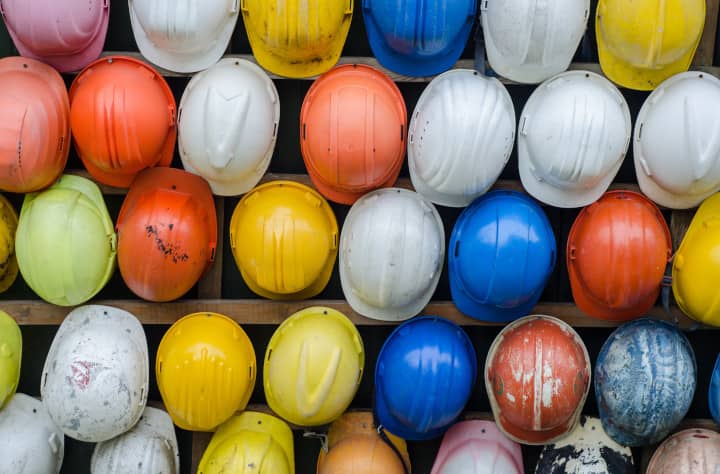
Welding safety datasheets
Safety datasheets contain information on the hazards associated with welding, and the control measures that should be in place to minimise the risks.
Welding safety posters
Safety posters can be used to raise awareness of welding hazards and the importance of following safe work practices.
Welding safety signs
Safety signs can be used to remind employees of the dangers associated with welding, and to indicate the location of safety equipment.
Regulatory bodies
You can contact your local regulatory body for information on welding safety regulations. In Australia each state has its own regulator and legislation.
Industry associations
You can contact your local industry association for information on welding safety best practices. In Australia, the relevant industry association is the Australian Welding Institute (AWI).
Conclusion
In conclusion, it is important to be aware of the hazards associated with welding, and to take steps to minimise the risks. By using the hierarchy of control, following the safety procedures and using the right PPE, you can help to ensure that your employees are safe while they are working and that welding safety is not an issue in your workplace.
How can Safe-R Outcomes help your business?
Safe-R Outcomes has a range of safety documents to help improve your welding safety including safety manuals, toolbox talks, checklists and registers.
Our Professional subscriptions contain many essential documents including:
- WHS Management Plans / Safety Manuals
- SWMS (if the job entails high risk tasks)
- a range of SOPs, Registers, Toolbox Talks, Checklists and Policies
These can all be downloaded and are not blank templates, so can be used immediately.
We also provide Induction training to help you on-board new employees and contractors.
As you can see it is all done for you so it makes it nice and simple. You can find out more on the Industries and Professions page.
If you’re concerned about the time commitment and knowledge required to implement the correct documents, procedures and training for forklift safety, Safe-R Outcomes can help. We strive to reduce the time and cost for businesses to implement their legally necessary safety requirements.
1 Comment
Jony · 30/04/2023 at 2:48 pm
Hey,
your welding safety tips made working with my welder easier. Thanks for sharing your experience.
Comments are closed.