What is the hierarchy of control?
The ways of controlling risks are ranked from the highest level of protection and reliability to the lowest. This ranking is known as the hierarchy of control.
The hierarchy of control is how we decide what control measures should be used when completing a risk assessment. It is a hierarchical list of six different types of controls that are ranked, with the most effective control at the top of the list. Generally we refer to it as the ‘hierarchy of control pyramid’.
One thing that often surprises people is that PPE is not the best way to control the hazards and risks a worker may face. PPE is actually last on the hierarchy of control.
The hierarchy of risk control is a structured approach used across Australian workplaces to manage health and safety risks effectively. Referred to in legislation as the hierarchy of control WHS, it outlines the preferred order of methods to eliminate or minimise hazards. From the most effective, like elimination, down to administrative controls and PPE, this model helps employers choose the most reliable way to reduce risk. Sometimes called the hierarchy of hazard control, this framework ensures that all hazards are assessed and controlled with the most appropriate and legally compliant hierarchy of control measures available.
The six levels of controls are shown in the pyramid below:
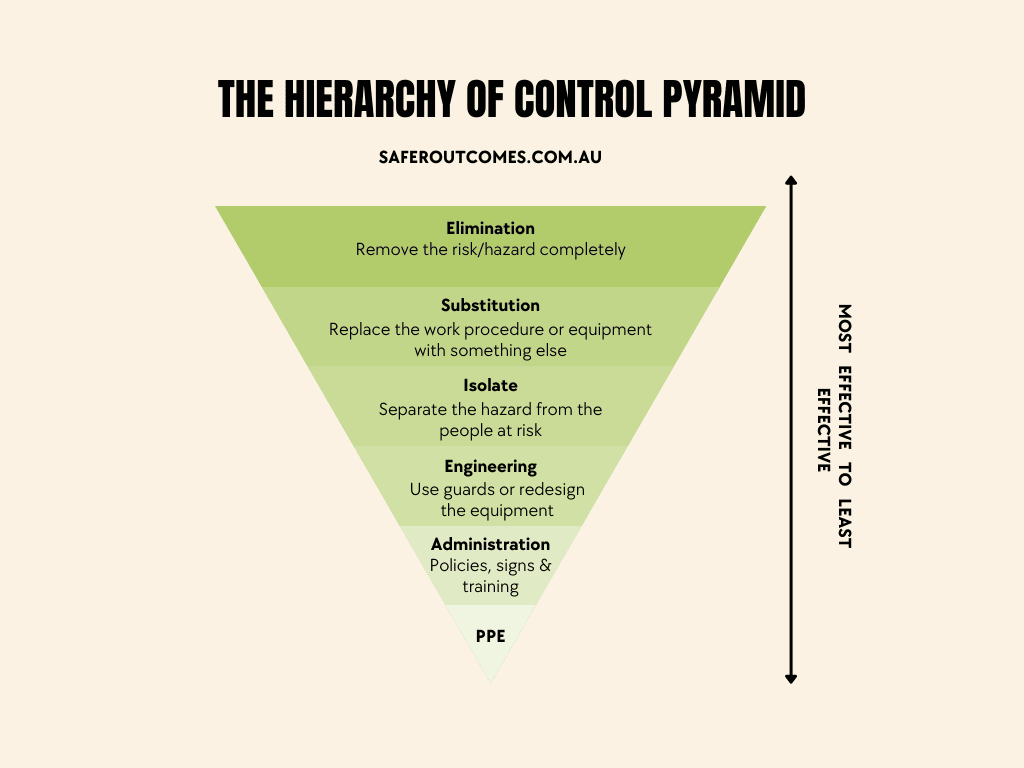
Why is the hierarchy of control important?
The hierarchy is important because it ensures that the most effective control measure is implemented first. If the top control is not feasible or appropriate, then the next one down on the list should be considered. This will reduce risk to a low enough level that there should be no reason to implement any other control.
For example, if you have identified the hazard of breathing in silica dust, then the most effective way to control this hazard is to avoid it happening altogether by not using products that contain silica. If that is not possible, then you would continue down the hierarchy of control until you have implemented as many controls as possible so the risk to workers is as low as possible.
The hierarchy of control also creates an understanding that not every hazard or risk can be completely eliminated, so it allows for other control measures to be put in place.
It is important to remember that these are not the only six types of control measures used within risk management – there are many others. But it is a good place to start so you can ensure you are considering the most effective control measures first.
The hierarchy of control is listed in order from the least to most risky, so PPE being at the bottom shows how important it is to have all other controls in place before using any protective equipment.
Hierarchy of Control Levels
1. What does Elimination Controls mean?
Starting at the top of the pyramid, we have elimination. Elimination is when we remove or reduce a hazard from an activity to such an extent that it no longer exists. This is obviously very effective, but can often be very difficult and costly to implement. However, sometimes it can be as simple as changing the way work is done, as an example using a drone to check for damage on a roof rather than climbing on to the roof and walking around and risking a fall from height. Elimination is the best control measure and should be used whenever possible.
2. What does Substitution Controls mean?
Second on the hierarchy of control pyramid is substitution. This is where we swap out a hazard or risk in an activity for something that does not pose the same level of risk. It is also another very effective control measure, but for this reason, it can often be difficult to implement.
For example, while gardening you find a lot of weeds, so the task is ‘Killing weeds’. Now instead of using a highly toxic weed killer, you could choose to use a different weed killer which is less harmful to the environment and safer for yourself.
This is substitution because you are still performing the task of killing weeds, but you have substituted the toxic chemicals with chemicals that poses less risk, or no risk at all. But if you decide to manually pull the weeds out, this is elimination as you are eliminating the need to use weed killer altogether even though you are still performing task of killing weeds.
3. What does Isolation Controls mean?
The third control measure in the hierarchy of control pyramid is isolation/confinement. This is when a hazard or risk in an activity is restricted to a small area so any risk is limited to that area. It may only be temporary, but it still greatly reduces the risks outside this small area. A common example most people would have seen is when an x-ray is performed in a room and the radiographer moves into a special room for each x-ray.
4. What does Engineering Controls mean?
The fourth level of the hierarchy of control is engineering controls. These are physical devices which can be used to minimise risk. The simplest example would be a guard on a machine to protect against contact with a rotating blade. Also, by considering the shape of equipment and how it is used from a safety perspective, you can often find opportunities to improve safety within the machines design without having to add any additional controls or devices.
There are many types of engineering control that exist, and they all provide different levels of safety depending on the risk they are mitigating. They are all designed to stop or minimise hazards, but often may not completely remove them entirely.
5. What does Administration Controls mean?
The fifth level on the hierarchy of control is administrative controls. With administrative controls, we provide specific instructions that say how an activity should be performed in a safe way. This can range from procedures, information and training for individuals completing an activity, to signs and labels for equipment and hazardous areas. This is not very effective as it relies on people always doing the right thing or being trained effectively.
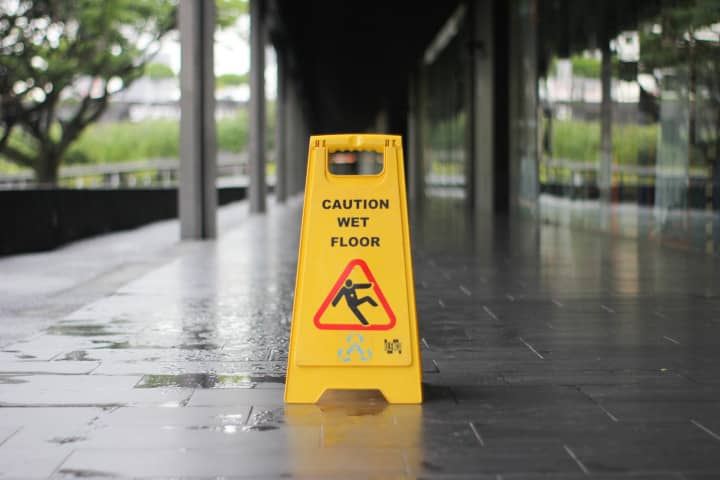
Administrative controls can be further divided into:
- Behavioural controls which are designed to influence how people think and act. These could be rules or procedures that people must follow in a certain order, as well as the behaviour of individuals at work. Training is a classic example of a behavioural control to ensure employees perform tasks safely.
- Environmental controls operate externally by controlling the environment around an activity. This could be anything from managing access to a certain area, controlling the noise levels and/or visual distractions around the work area or creating safe storage for dangerous equipment and chemicals.
- Supervisory controls are concerned with making sure that workers are suitable for the task they are about to carry out. This means providing them with training, information and instruction specific to the task or job role they are doing. Supervisory controls can range from the management of risk assessments, mandatory regular breaks or regular competency testing. Mandatory regular breaks are a good example of supervisory control. They are used to minimise the risk of fatigue by providing short periods away from the task so that workers can rest and recuperate, preventing any drowsiness which could cause harm.
Administrative procedures can also be very effective, such as reviewing critical incidents and near misses after an incident. This can help to determine if there any systemic issues that contributed to the occurrence of the hazard, or to learn lessons that can be shared within or between work groups, organisations or companies.
The most common example is the use of a safe system of work to guide workers on how to carry out tasks in a safe manner. Administrative controls are not designed to stop or minimise hazards, but they do reduce risks by providing specific instructions on how to carry out activities safely and in a controlled manner. Administrative controls also provide the opportunity to monitor and track tasks, ensuring that workers are following these instructions.
6. What does Personal Protective Equipment (PPE) mean?
The sixth, and final level of the hierarchy of control is personal protective equipment. While personal protective equipment has a very negative connotation for many people because there are so many examples where it is misused and overused, it should only ever be used as a last resort.
The most common everyday example is wearing sunscreen when outside to reduce the risk of skin cancer, or an enclosed hard-hat on construction sites where there is a risk of falling objects. Another example would be safety goggles to protect the eyes from splashes and dust.
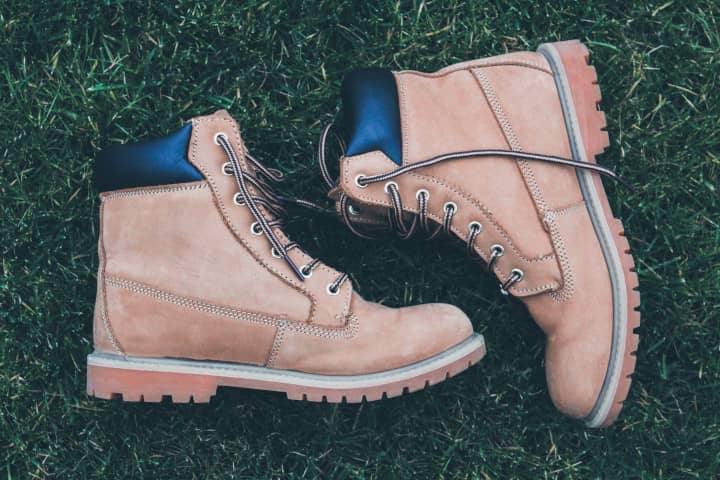
Personal protective equipment includes any special clothing or device worn by people which protects them from harm. These are commonly things like rubber gloves, safety glasses, ear plugs etc. It would be extremely difficult to complete tasks without the use of PPE; however they are not always suitable or practical for every task. For instance, it is not practical to wear steel-capped boots while doing concreting or walking on a roof, and could actually be dangerous.
This article has explained what the hierarchy of control is and why it is important for workplaces. The hierarchy of control is a structure which indicates the best way to control risks at any given time, starting with the most effective control methods and ending with the least preferred method. This is based on the idea that it is better to use one or more controls together than just one single control.
Hierarchy of Control Toolbox Talk
When it comes to controlling risks in the workplace, there is a specific order or hierarchy that should be followed. Unfortunately, many workers (even in high risk roles) don’t know about it and that is where a toolbox talk can be helpful. Toolbox talks are a great way to engage workers in a discussion about health and safety risks and how to control them.
They also provide an opportunity for workers to ask questions and raise concerns. It is also important as a business owner to show that you are trying to manage risk and meet your legal obligations. You can do this by making sure that all attendees sign a toolbox talk register, which you can use as evidence should the need arise.
5 Toolbox Talk hints and tips to make your life easier will help you give better toolbox talks, and improve workplace safety.
Choosing Effective Risk Controls Within Hierarchies
When choosing risk controls, consider the following factors:
Risk Severity: The potential impact and likelihood of the risk.
Cost-Benefit Analysis: The cost of implementing the control versus the potential savings from risk reduction.
Effectiveness: The control’s ability to mitigate the risk.
Feasibility: The practicality of implementing the control.
Regulatory Compliance: The need to adhere to industry regulations and standards.
A Hierarchical Approach to Risk Control
- Prioritize Risks: Identify and assess the most critical risks to the organization.
- Apply Higher-Level Controls First: Start by considering elimination or substitution, as these are often the most effective ways to manage risk.
- Combine Controls: Use a combination of controls from different hierarchies to create a comprehensive risk management strategy.
- Regular Review and Update: Periodically review and update your risk controls to ensure their continued effectiveness.
By understanding the six hierarchies of control and following a systematic approach, organizations can effectively manage risk and protect their assets and reputation.
How often should a hierarchy of control toolbox talk be given?
Ideally, a toolbox talk should be given on a regular basis, at least once per month, if not at least once per week. However, specifically a hierarchy of control toolbox talk should be given at least once per year or when new staff are put on the team. This will ensure that workers are kept up to date with the latest information and that they are reminded of the importance of following the hierarchy of control and are able to ask questions if they aren’t sure about anything.
How can Safe-R Outcomes help your business?
Our Professional subscriptions contain many essential documents including:
- WHS Management Plans / Safety Manuals
- SWMS (if the job entails high risk tasks)
- a range of SOPs, Registers, Toolbox Talks, Checklists and Policies
These can all be downloaded and are not blank templates, so can be used immediately.
We also provide Induction training to help you on-board new employees and contractors.
As you can see it is all done for you so it makes it nice and simple. You can find out more on the Industries and Professions page.
If you’re concerned about the time commitment and knowledge required to implement the correct documents, procedures and training for forklift safety, Safe-R Outcomes can help. We strive to reduce the time and cost for businesses to implement their legally necessary safety requirements.