You may have heard the term PPE at work or on the news, or maybe you’ve been told to get some PPE to do certain tasks and have no idea what it means, or why it is so important. After reading this article you will know everything you need to know about PPE.
What does PPE stand for?
PPE stands for Personal Protective Equipment.
What is PPE?
PPE also known as Personal Protective Equipment is any clothing or equipment worn by workers to minimize exposure to workplace hazards. PPE includes items such as safety glasses, gloves, earplugs, hard hats and respirators.
Workers in different industries have very different types of PPE depending on the risks they face on the job. For example, construction workers are more likely to need hard hats than people who work in an office, while chemical workers may need to wear respirators or other types of breathing equipment. Even workers in a fast food restaurants use it, such as leather shoes and aprons.
PPE can help safeguard against a variety of risks, including physical dangers, chemical hazards, and infection. Whether you’re working in a factory or a hospital, it’s important to know how to properly use and care for your gear. In order to stay safe on the job, always make sure that you are using the right type of protection for the task at hand.
If you’re a business owner, your first priority should be to ensure that your workers are protected. That means it’s important to provide them with the right PPE for their jobs.
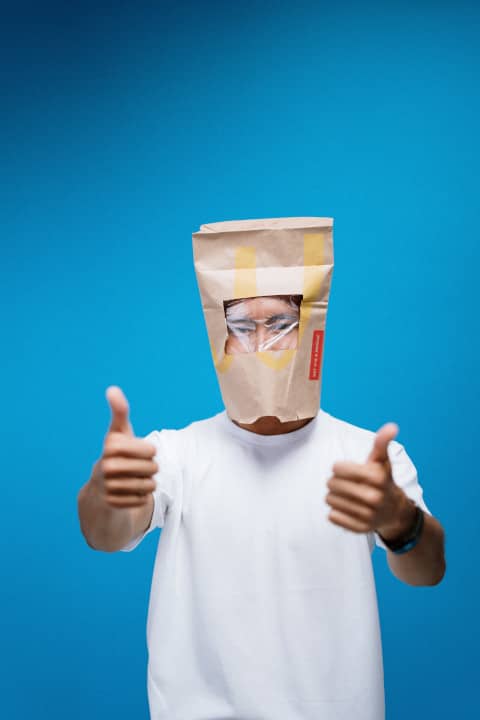
Do I need PPE?
Most of the time, employers provide PPE for their employees. But in some cases, it is up to the individual employee to meet company standards-for example, your employer may give you a hard hat but not require you to wear it. In this case, you should always wear the PPE to avoid consequences of not wearing it.
PPE is used in all kinds of workplaces, but the most common types are construction sites, chemical plants and laboratories. If you work in any of these types of places or other high-risk environments, it’s important to know how to use PPE correctly so that you can stay safe on the job.
Many PPE items are designed to fit a specific body part or be used in a certain way. In many cases, the equipment must fit the user correctly in order to work properly. For example, you can’t protect your eyes effectively if your safety glasses don’t fit right. If you’re unsure of how to use a piece of PPE, ask your supervisor for advice.
Some PPE is mandated by law, some is just expected. But remember, PPE is the lowest way to control risk according to the hierarchy of control. But that doesn’t mean it doesn’t have an important part to play in keeping workers safe.
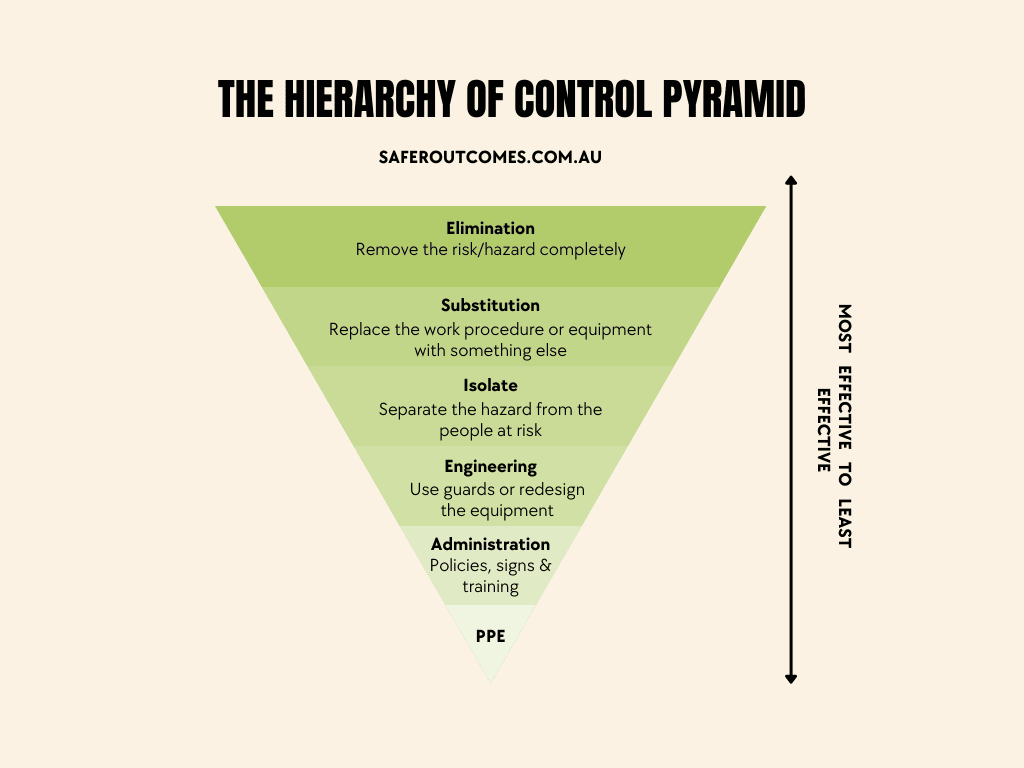
Why is PPE important?
Personal protective equipment serves three main purposes:
- It protects the wearer against injuries and death
2. It reduces potential hazards for the wearer
3. It protects other people nearby from the potential hazards
Wearing or using PPE is important because it is the easiest and most common way to reduce health and safety risks for workers. But again, it’s important to remember that using PPE is not the only form of controls against hazards and risks that should be in place. The risks should also be reduced in other ways using the hierarchy of control when completing a risk assessment (or a SWMS).
What are some types of PPE?
There are many types of personal protective equipment used to minimise worker exposure to injuries and hazards. PPE can be made in many different shapes and forms, but its main purpose is to reduce the risk of injury. It may protect the wearer from injury caused by falling objects or substances, or it could act as protection against chemical or biological hazards. It can also be used as a form of identification such as when high visability clothing is required.
The most common examples include:
- Gloves
- Goggles and face masks
- Earplugs and hoods or hairnets
- Earplugs or earmuffs for loud noises
- Hard hats and safety footwear
- Respirators, such as dust masks to protect against harmful substances in the air
- Sunscreen, hats and long sleeved shirts are also forms of personal protective equipment to protect against sun exposure when working outside.
Do I have to wear PPE?
Yes. If legislation or your workplace mandates specific PPE you must wear PPE. Not wearing it is dangerous because it can increase the risk of injury or illness related to hazardous materials or processes. It could even mean that health and safety standards are breached depending on the nature of work.
Some types of machinery, tools, equipment and chemicals also require PPE to be worn in their user agreement or instruction manual. It is important that all workers read both the legislation and the user manual before using any equipment.
Some people will have to use modified forms of PPE such as prescription safety glasses. In this case, suitable prescription glasses or lenses will need to be purchased. But, you still need to wear it if it is required.
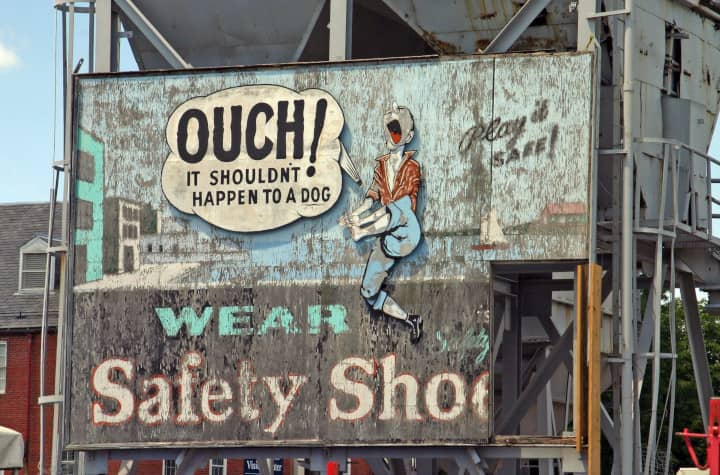
Who makes the decision about what PPE I have to use?
The employer has to assess the risks involved in your work duties. They then decide on what type of personal protective equipment you should wear while completing these tasks. It’s important that you follow these rules and that you don’t work without the appropriate PPE.
What happens if I don’t wear the right PPE?
It’s against the law to not use or wear PPE in certain situations, especially where legislation has been implemented. If legislation is in place to protect workers using PPE, then it is an offence not to comply.
If there’s no specific legislation in place, you still risk breaching health and safety standards if you don’t wear PPE required by your workplace. This could mean that a number of measures are taken against the business or individual including disciplinary action, a fine or a claim for compensation. Legislation states that you must follow all reasonable safety directions, and wearing PPE is a reasonable direction (unless it puts you at more risk by impeding your ability to work safely).
So if you don’t wear your PPE as directed you may be suspended or dismissed from your work. And if you are injured while not wearing your PPE, you may find that any claim you have for compensation against your employer is denied. Plus, if your actions also caused injury to others, you may also find that you are fined or charged by the regulator in your state.
When do I need PPE?
You need PPE if:
- Your training/licence requires specific PPE to be worn to comply with the legislation of your job role;
- You are required to wear PPE under an agreement with your employer, for example by using certain tools or equipment;
- Your workplace has signs that say “Wear Personal Protective Equipment (PPE)”;
- You are undertaking work where there is a risk of injury or illness to yourself or others;
- You are working in extreme weather conditions or hazardous working environments;
- Your workplace/job role requires it by law.
When you need PPE, you might have to wear it all the time while at work or just when carrying out specific tasks. If you don’t wear prescribed equipment correctly this may not provide the protection required and could increase the risk of an accident happening to you or others.
Remember, not all injuries can be seen so PPE acts as a preventative measure before you are injured.
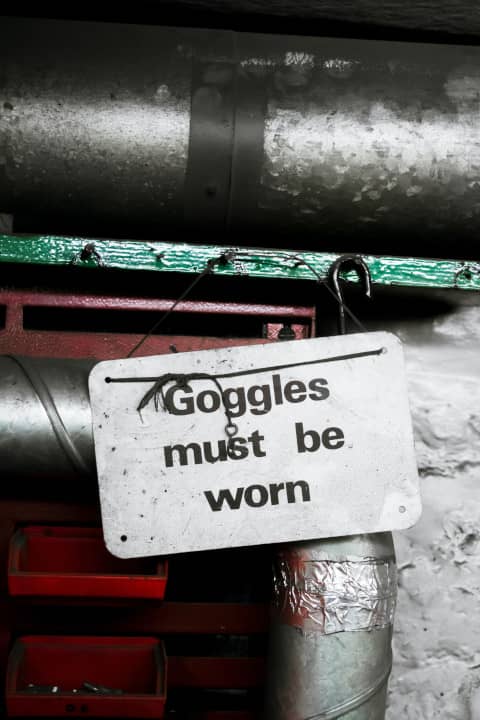
What if I don’t have the right PPE?
If you do not have the correct equipment then speak to your supervisor about what equipment is available. They may not be able to provide it immediately but they should be able to help you get it. If you don’t have the correct PPE or it is not fit for purpose because of damage, or because it doesn’t fit you, you must stop work immediately.
A PPE supplier or manufacturer should be able to advise you of the correct type of equipment required for your work. If their advice is not suitable, then speak with your supervisor and let them know why you do not feel safe working in that environment without the correct equipment.
Is PPE expensive?
PPE can be expensive, but there are ways to save money when buying equipment by shopping around and using online resources. Purchasing equipment in bulk can also be cheaper. PPE may seem expensive but the cost of medical treatment or missing work because you are injured is more expensive. Employers must supply mandated PPE, but if you require additional PPE then you must purchase it yourself. In most cases you can also use PPE purchases as a tax deduction on your tax return.
How often should I replace PPE?
Some PPE will be obvious when it’s time to replace them, for example when they are faulty or ripped. However, if there isn’t any damage, you should still check the expiry dates on your equipment. Before using new equipment, always read the manufacturers’ instructions and never assume that all types of PPE are safe to use. Some PPE has a life span and should be replaced if it is no longer effective.
The expiry dates on your PPE will vary depending on the type of equipment you have. After that time, any impact it had as a protection measure will reduce significantly. It’s important to keep an inventory of all the PPE you use for your job in case there is an accident or incident. Take photos of your PPE and keep them in a central location like a PPE register.
PPE is a very useful tool in protecting workers from workplace hazards that can cause serious long-term damage or even death. However, it must be used properly in order for it to work correctly. PPE is not a substitute for good work practices or safe working conditions, and must always be used together with them in order to best protect workers. A worker might still get hurt even if they are wearing PPE. This is not because it doesn’t work, but because the worker has failed to use it correctly or their work environment puts them in more danger than the equipment they wear can protect them from.
PPE Toolbox Talk
Toolbox talks are a great way to share information about PPE with your workers. They provide an opportunity for you to talk about the importance of using PPE and how to use it correctly. Toolbox talks also allow workers to ask questions and give feedback about their PPE experiences.
When conducting a toolbox talk on PPE, there are a few key points that you should cover, so read 5 Toolbox Talk hints and tips to make your life easier for more information.
How often should I give a PPE toolbox talk?
Some places of work give a short toolbox talk at the beginning of every shift, however, this isn’t always possible or practical. Toolbox talks should be given as often as is necessary to keep workers up-to-date with changes in legislation, new types of PPE that are available, or changes to the way that PPE is used in your workplace.
How can Safe-R Outcomes help your business?
Our Professional subscriptions contain many essential documents including:
- WHS Management Plans / Safety Manuals
- SWMS (if the job entails high risk tasks)
- a range of SOPs, Registers, Toolbox Talks, Checklists and Policies
These can all be downloaded and are not blank templates, so can be used immediately.
We also provide Induction training to help you on-board new employees and contractors.
As you can see it is all done for you so it makes it nice and simple. You can find out more on the Industries and Professions page.
If you’re concerned about the time commitment and knowledge required to implement the correct documents, procedures and training for forklift safety, Safe-R Outcomes can help. We strive to reduce the time and cost for businesses to implement their legally necessary safety requirements.