If you’ve been asked to do a risk assessment in your workplace and have no idea how to get started, or maybe you’ve just heard the term but aren’t sure what it means, this is the article for you.
What is a risk assessment?
A risk assessment is a procedure to identify potential problems and decide how risky they are. The aim of a risk assessment is to reduce the probability or consequence of harm. A risk assessment can be applied to both physical and informational hazards, in this context we are talking about workplace safety risk assessments.
In Australia, Safe Work Method Statements are a kind of risk assessment.
A lot of information must be known to do a risk assessment, for example what are the possible failures in the system? How often could this happen? What is the impact of failure/by-product? When will this happen? What can be done to eliminate or reduce the risks associated with it? However, it is not as difficult as it seems, especially if you have an experienced worker complete the risk assessment process.
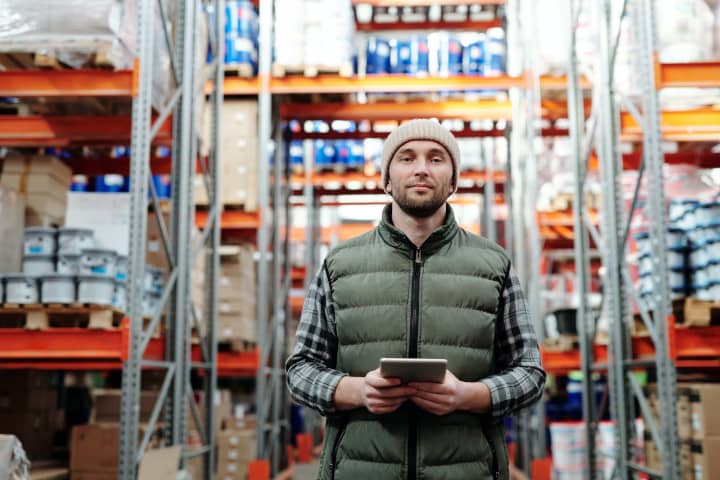
Certain hazards may be eliminated or reduced by simple, low cost interventions when the risk assessment process is completed. Other risks may require more extensive and costly countermeasures (such as technology). Some hazards can be easily monitored; others will require specialized measurement equipment, special training of personnel and/or technical expertise.
However, by completing the risk assessment process for each task or piece of equipment , you can identify the hazards that may arise and then devise appropriate actions to address them.
From an organisational perspective, risk assessments are often used to inform decision-making by identifying critical issues, estimating the probability of mishaps occurring across different scenarios and evaluating countermeasures against potential losses due to accidents.
A risk assessment is a key part of a formal safety management system and a requirement under a range of international standards.
For most companies, risk assessments involve more than identifying hazards; they typically include estimating the probability of an incident occurring (the risk) and evaluating the severity of potential injuries or other losses.
Companies will often use risk assessment tools to establish which hazards are critical, define measures to prevent accidents and establish optimal solutions within cost constraints.
Risk assessments also mean that employees have access to knowledge that can help keep them safe when they are doing their job. A risk assessment can help workers be safe by showing them what needs to be done and why.
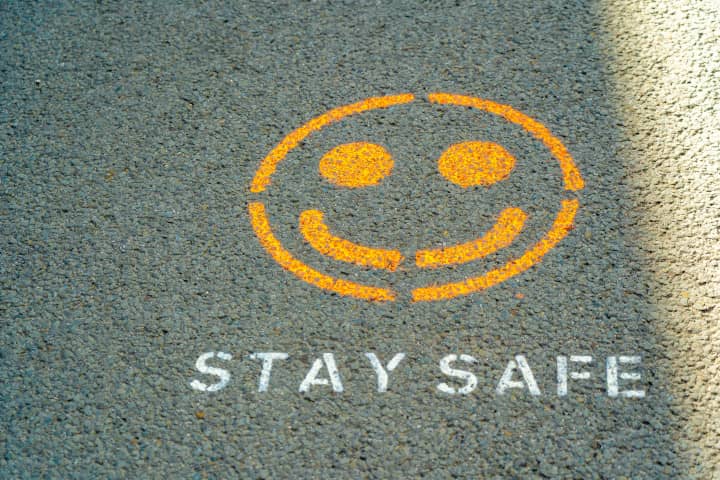
The risk assessment process aims to identify, assess and control risks in order to avoid accidents and minimise their impact on people and property. A well-documented risk assessment provides the basis for an organisation’s work environment compliance system which can also help reduce risks.
Risk assessments often focus on how to keep people safe. But two other elements also need to be considered: how the work affects the environment and whether it is likely to cause damage to property, either through accidents or by bringing about harm that could have been foreseen.
Risk assessments are essentially some of the foremost useful tools for any contemporary business which will endeavor to successfully adapt itself within the market which now expects workers to be safe at work. These risk assessments help companies in identifying what potential hazards or threats can affect its existence and accordingly, take proactive steps to neutralize the risks.
Whether it’s designing new products, updating existing ones or modifying the way work tasks are carried out: Risk assessment can be applied to almost any business process that will significantly impact the business.
In Australia, risk assessments provide evidence that you are managing your safety obligations which is required under work health and safety legislation.
Every company is different, so the way a risk assessment is carried out can vary depending on the organisation’s size and structure. A small business may have a committee with 3-5 members who represent all areas of the business to assess risks.
In some organisations, one person will be responsible for completing most assessments. In these situations it is important that a second person is involved to provide an external review of the risk assessment.
Risk assessments need to be done in a way that involves everyone who does that job or uses that equipment. This can vary from one risk assessment to another, but people should have the opportunity to:
- be a part of the risk assessment process,
- give their input into the actual risk assessment, and
- vote on whether they are happy with the findings.
What is the risk assessment process?
A risk assessment is a decision making tool that enables the user to identify potential problems.
The risk assessment process typically includes:
1. Identify the accident/incident sources (i.e. what can go wrong)
Firstly in the risk assessment process you need to identify the accident/incident sources. These are what can go wrong during a certain activity, and often there is more than one of these for any given risk. You also need to identify how an accident or incident could happen – this is the mechanism of injury. For example climbing a ladder you could fall off, the ladder could collapse, or you could drop something from your hands. Then you need to decide how this could happen which might include, not using 3 points of contact, not using the right ladder for the job or carrying too much.
2. Evaluate the severity and likelihood of each accident/incident source
Secondly, you need to determine the severity and likelihood of each risk – how serious could it be? How likely is it that this will happen ? Sometimes after working your way through an assessment you may find that there is no risk at all. This just means that there are no accident/incident sources or they have very low severity and likelihood. It can also be difficult to decide how likely an incident will occur or how severe the consequences can be.
Again, going back to falling off the ladder it could depend on which run of the ladder you are on, what the ground is like below you and whether you have other ailments that could contribute to injuries.
Also, when deciding the severity and likelihood of each accident/incident source, keep in mind that your decision might change over time as the company changes and the equipment used may change. In this case it would be wise to reassess risks from time to time.
The main thing to consider is that most tasks pose a risk in one way or another before controls are put in place, so don’t just say that everything is low risk just to get the job done. It might come back and bite you at a later date.
3. Decide what needs to be done about each risk
Then, you need to decide what action is needed for each risk – how it will be managed. We call this a control measure. There could be control measures that are appropriate in one situation; it is up to you to decide what is the most appropriate. Don’t just choose the easiest solution. You can use the hierarchy of control to help you decide what will keep your workers the safest.
Remember, safe workers take less time off work through injury, and it also means tools, equipment and materials are less likely to be damaged and need to be replaced.
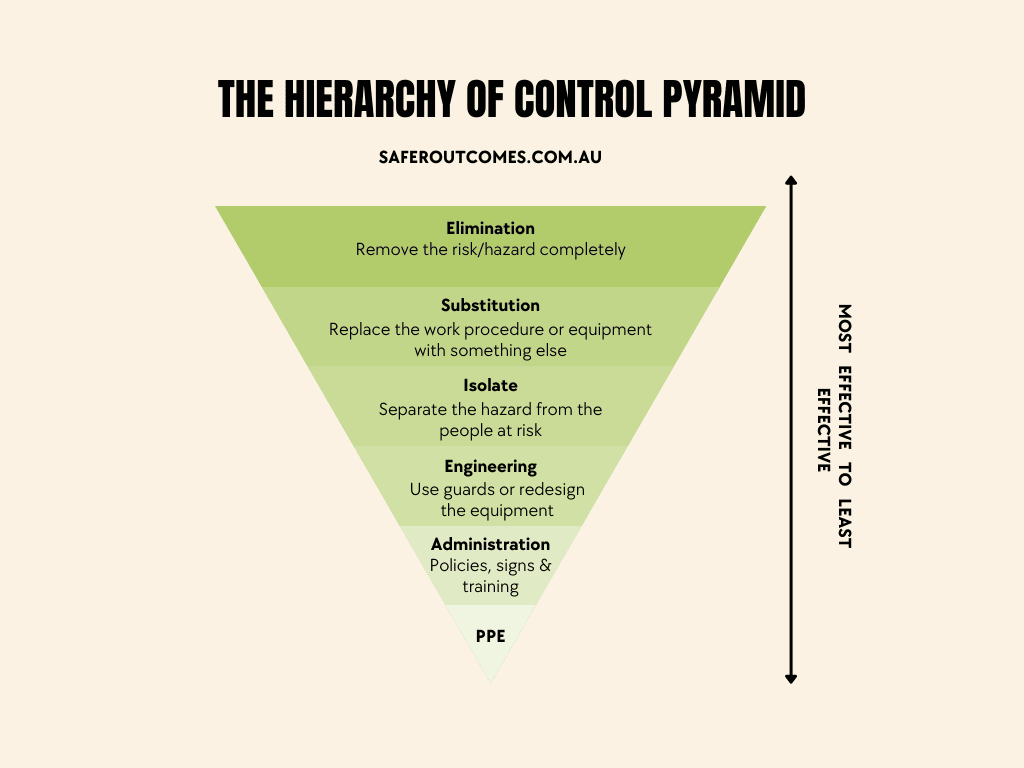
4. Implement your controls
Now, it is important that you take action on what you have decided – controlling the risk or making it safer. There are many ways this can be done but all actions should be effective in reducing the likelihood and severity of an accident/incident source.
For some activities there may be more than one accident/incident source, or multiple accidents/incidents that could happen. In this situation you need to choose the most important one and make sure it is dealt with first. This is known as a “key accident/incident source”.
5. Review your control measures
It is also important to review the control measures you have put in place. This will tell you whether or not they are effective and if not, what needs to be done differently. Sometimes the control measures we implement actually end up making things more risky or when put into practice, just don’t work at all. In this case we need to change the control measures, or decide that it is not necessary to implement them in the first place. This where talking to experienced workers can reduce the chances of having to repeatedly go through these steps.
What is a risk assessment matrix?
A risk assessment matrix is the table that is used to understand the risk ratings associated with the risk assessment process. Each column in the risk matrix represents an accident/incident source, while each row represents the severity and likelihood of an accident/incident. The intersection of a column with a row shows what the risk rating of each task or item is. For example, a task rated as “high” for severity and likelihood would have a risk rating in the intersection of a column with a row that is “very high”. There are five risk ratings: very low, low, medium, high and very high.
By using the risk assessment matrix we can easily get a better understanding of risks associated with the work to be completed.
Necessary action is then undertaken to reduce the severity and likelihood of the accident/incident.
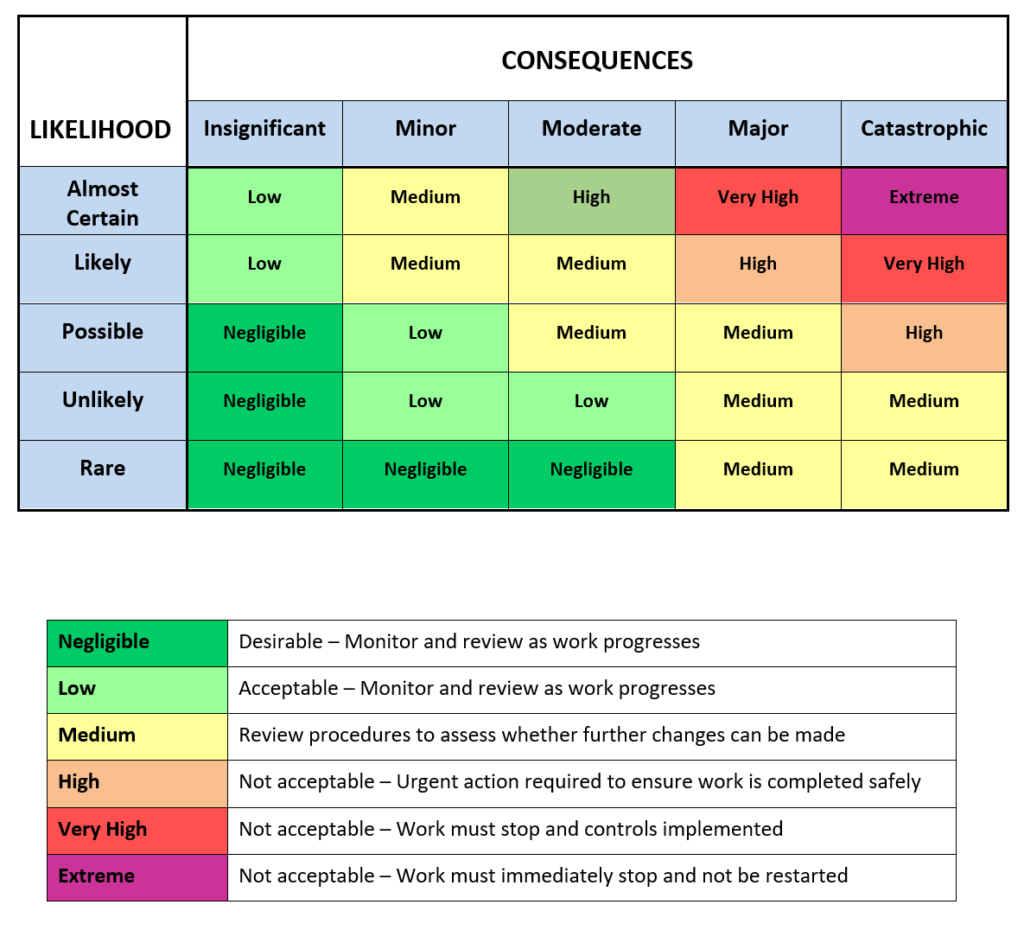
So now that you have considered all of this it’s time to apply these steps to your own business/workplace. Risk assessments must be done for all health and safety risks that means there is a chance of injury from entering or being in an unsafe situation. This includes work equipment, workspaces, processes and chemicals.
It’s a good idea to do a risk assessment every time work routines, tools or conditions change so you can see if there are any new hazards. You should always assess risks before starting an equipment, process or task that has the potential to cause injury.
It can also be useful to have a chat with your workers and find out how they feel about the risks and their job. Maybe, some of them can offer you ideas that will help to eliminate or minimize certain risks. They might also give you feedback that allows you to go back and review risks very quickly. So remember,
1. Identify the hazard
2. Evaluate the severity and likelihood of each accident/incident source,
3. Decide what needs to be done about each risk,
4. Implement your controls, and
5. Review your control measures!
Then you can be sure that the risk assessment process is not only efficient but also useful for both you and your workers.
The Importance of Safety Risk Assessments in the Workplace
A safety risk assessment is a proactive approach to identifying and mitigating hazards in the workplace. It is a structured process aimed at safeguarding employees, contractors, and visitors by systematically evaluating potential risks and implementing effective control measures.
Why Conduct a Safety Risk Assessment?
- Prevent Workplace Accidents: By identifying hazards early, businesses can take steps to prevent injuries and incidents.
- Ensure Legal Compliance: In Australia, safety risk assessments are essential for adhering to Work Health and Safety (WHS) regulations.
- Enhance Employee Well-being: A well-executed assessment promotes a culture of safety and boosts worker confidence.
- Reduce Financial Liabilities: Avoid costly penalties, insurance claims, and downtime caused by workplace accidents.
Key Components of a Workplace Risk Assessment
- Hazard Identification: Recognize potential risks in the workplace, including physical, chemical, biological, and ergonomic hazards.
- Risk Evaluation: Assess the likelihood and severity of identified risks to prioritize control measures.
- Control Implementation: Apply strategies to eliminate or reduce risks, following the hierarchy of controls.
- Monitoring & Review: Continuously review and update the risk assessment to reflect changes in the workplace environment.
How Safety Risk Assessments Improve Workplace Safety
Conducting regular workplace risk assessments creates a safer environment by actively managing potential hazards. It empowers employees to recognize risks and take appropriate actions, fostering a proactive safety culture that benefits both staff and management.
How can Safe-R Outcomes help your business?
Our Professional subscriptions contain many essential documents including:
- WHS Management Plans / Safety Manuals
- SWMS (if the job entails high risk tasks)
- a range of SOPs, Registers, Toolbox Talks, Checklists and Policies
These can all be downloaded and are not blank templates, so can be used immediately.
We also provide Induction training to help you on-board new employees and contractors.
As you can see it is all done for you so it makes it nice and simple. You can find out more on the Industries and Professions page.
If you’re concerned about the time commitment and knowledge required to implement the correct documents, procedures and training for forklift safety, Safe-R Outcomes can help. We strive to reduce the time and cost for businesses to implement their legally necessary safety requirements.
Q1: What is a risk assessment?
A risk assessment is the process of identifying hazards in a workplace, evaluating the risks associated with them, and determining appropriate ways to eliminate or control the risks.
Q2: Why is risk assessment important in the workplace?
It helps prevent accidents and injuries by ensuring hazards are identified early and mitigated with suitable control measures. It also helps meet WHS legal obligations.
Q3: Who is responsible for conducting a risk assessment?
Employers, managers, supervisors, and health and safety representatives typically conduct risk assessments. However, workers may also contribute by reporting hazards.
Q4: What are the 5 steps in a risk assessment?
- Identify the hazards
- Assess who might be harmed and how
- Evaluate the risks and decide on control measures
- Implement the control measures
- Review and update the assessment regularly
Q5: How often should a risk assessment be reviewed?
Risk assessments should be reviewed regularly, especially when there is a significant change in the workplace, an incident occurs, or new equipment or processes are introduced.
Q6: What is the difference between a hazard and a risk?
A hazard is something that has the potential to cause harm (e.g., chemicals, machinery), while a risk is the likelihood that harm will occur from the hazard.
Q7: Do I need to document my risk assessments?
Yes, especially for high-risk activities. Proper documentation shows compliance with WHS regulations and provides a reference for reviews and audits.