A Safe Work Method Statement (SWMS) is a critical document required for high-risk construction work (HRCW) in Australia. It serves as a roadmap for identifying hazards, assessing risks, and implementing control measures to ensure workplace safety. Many industries, from construction and landscaping to manufacturing and logistics, rely on SWMS templates to standardize safety procedures. Without a compliant SWMS, businesses risk legal penalties, workplace accidents, and project delays. In this guide, we’ll explore the importance of SWMS templates, which industries need them, how to create an effective SWMS, and real-world case studies of businesses that have benefited from using them.
What is an SWMS Template?
An SWMS template is a pre-structured document that outlines the steps required to complete high-risk tasks safely. It includes hazard identification, risk assessment, and control measures that must be implemented to minimize potential dangers. A well-designed SWMS template ensures that all workers follow the same safety standards, reducing the likelihood of accidents and compliance breaches. By using a structured template, businesses can streamline safety procedures, improve communication, and ensure that workers clearly understand their responsibilities before beginning high-risk tasks.
Who Needs an SWMS Template?
SWMS templates are mandatory for jobs classified as high-risk under Work Health and Safety (WHS) regulations. These include roles in:
- Construction & Trade Work – Builders, electricians, plumbers, roofers, painters who perform tasks at heights, use power tools, or handle hazardous materials.
- Landscaping & Outdoor Work – Gardeners, tree loppers, and fencing contractors who use heavy machinery, handle chemicals, or work near roadways.
- Civil & Infrastructure Projects – Excavators, demolition workers, and road crews exposed to unstable structures, underground services, or traffic hazards.
- Industrial & Warehouse Work – Factory workers, manufacturers, and forklift operators who handle heavy loads, hazardous chemicals, or operate dangerous machinery.
- Cleaning & Maintenance – Window cleaners, HVAC technicians, and commercial cleaners working at heights or handling toxic substances.
- Transport & Logistics – Truck drivers, freight handlers, and machine operators securing heavy loads or working around moving vehicles.
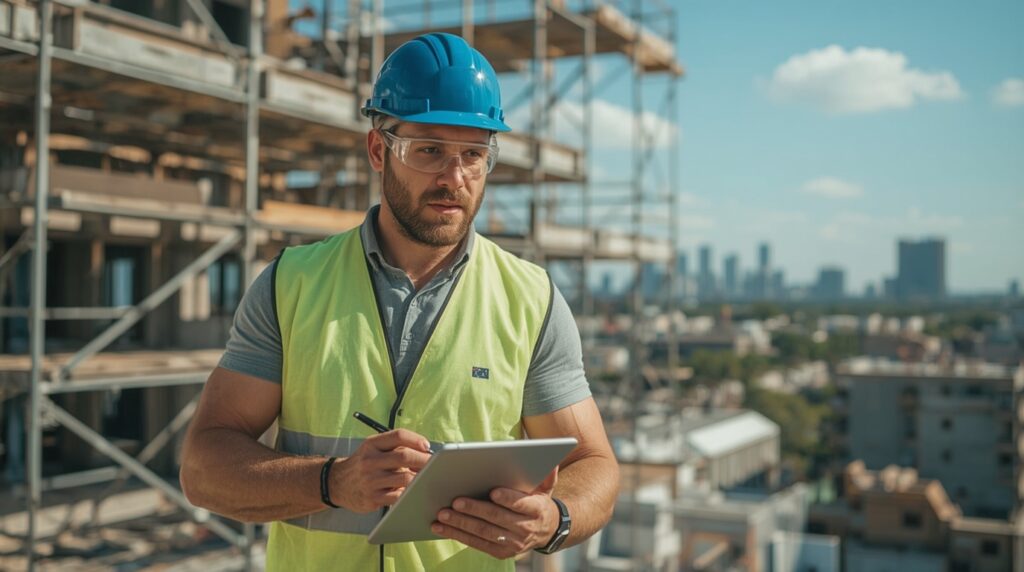
How to Create an Effective SWMS Template
Step 1: Identify High-Risk Work Activities
The first step in creating an SWMS template is identifying tasks that involve significant hazards. These may include working at heights, operating heavy machinery, exposure to hazardous substances, or working in confined spaces. Clearly defining each high-risk activity ensures that proper safety measures are in place to protect workers.
Step 2: Assess Hazards & Risks
Each identified task should have a corresponding list of potential hazards. For example:
- Electrical Work: Risk of electrocution, arc flashes, or exposure to live wires.
- Excavation: Trench collapses, underground utilities, soil instability.
- Tree Lopping: Falling branches, chainsaw injuries, improper harness use.
- Warehouse Operations: Forklift collisions, unstable racking, poor manual handling techniques.
Step 3: Implement Control Measures
Control measures should follow the hierarchy of risk control, including:
- Elimination: Removing the hazard where possible, such as replacing manual lifting with mechanical aids.
- Substitution: Replacing high-risk equipment with safer alternatives, such as using cordless tools instead of wired ones to prevent trip hazards.
- Engineering Controls: Installing physical barriers, safety rails, or ventilation systems to reduce exposure to hazards.
- Administrative Controls: Implementing training programs, warning signs, and operational guidelines to ensure safe work practices.
- Personal Protective Equipment (PPE): Requiring helmets, gloves, eye protection, respirators, and safety harnesses as necessary.
Step 4: Document the Safety Process
A comprehensive SWMS template should include:
- Company Details & Project Information – Identifies who is responsible for the work and where it is being performed.
- Description of High-Risk Work – Provides a clear outline of tasks considered hazardous.
- Hazard Identification & Risk Assessment – Details all potential risks and their likelihood of occurring.
- Control Measures & Safety Procedures – Lists how risks will be minimized and safety will be enforced.
- Worker Sign-Off for Compliance – Ensures all workers acknowledge and understand the SWMS before commencing work.
Step 5: Review & Update Regularly
Work environments change, and safety risks evolve. Regularly review and update your SWMS template to reflect new risks, incidents, or regulatory changes. Compliance checks and audits should be scheduled periodically to ensure ongoing adherence to workplace safety protocols.
Real-World Case Studies: The Impact of an SWMS
Case Study 1: Construction Company Avoids Major Fines
A mid-sized construction company in Sydney was audited by safety inspectors. Thanks to its well-documented and regularly updated SWMS, the company avoided costly penalties and demonstrated compliance, ensuring it could continue operating on government contracts.
Case Study 2: Landscaping Business Reduces Workplace Accidents
A landscaping firm implemented a detailed SWMS after experiencing several workplace injuries. Within six months, reported accidents decreased by 40%, and employee confidence in workplace safety increased significantly.
Case Study 3: Warehouse Operator Secures a Major Client
A logistics company successfully secured a long-term contract with a large retailer after showcasing its SWMS procedures. The retailer prioritized vendors with strict safety protocols, and the SWMS played a key role in winning the deal.
Frequently Asked Questions (FAQs)
1. How often should an SWMS be updated?
An SWMS should be reviewed regularly, particularly when new hazards are introduced or after workplace incidents occur.
2. Can a generic SWMS template be used for all jobs?
No, each SWMS should be customized to address specific risks associated with a particular job or worksite.
3. Is an SWMS required for low-risk work?
SWMS is only legally required for high-risk construction work, but it is a best practice for many industries.
4. What happens if I don’t have an SWMS?
Failure to have an SWMS in place for high-risk work can result in fines, legal action, and increased workplace accidents.
Additional Considerations for an Effective SWMS Template
- Integration with Other Safety Documents – An SWMS should complement safety management plans, risk assessments, and toolbox talks.
- Digital Accessibility – Storing SWMS templates digitally allows easy updates, access, and distribution among team members.
- Industry-Specific Customization – SWMS templates should reflect the unique risks and compliance needs of different industries.
- Real-World Case Studies – Showcasing examples of effective SWMS implementation can help businesses understand best practices.
A well-structured SWMS template is essential for workplace safety and legal compliance. Whether you’re in construction, landscaping, warehousing, or logistics, having a properly developed SWMS ensures your team operates in a safe and controlled environment. Investing in a detailed SWMS will not only protect your workers but also strengthen your business credibility, improve efficiency, and help you secure high-value contracts. If you need a professionally crafted SWMS tailored to your industry, contact us today to ensure compliance and workplace safety.