Workplace safety is a fundamental aspect of any successful organisation. By proactively identifying and addressing safety hazards, companies can prevent injuries, illnesses, and fatalities, ensuring a healthier and more productive workforce.
Ensuring workplace safety is crucial for the well-being of employees and the overall efficiency of any organisation. Accidents and injuries can have severe consequences, including financial losses, decreased productivity, and harm to employee morale. To create a safe working environment, it is essential to understand common workplace hazards and implement effective control measures.
This article explores the top 10 workplace safety hazards across various industries and provides practical control measures to mitigate these risks effectively. Additionally, it highlights the importance of the Hierarchy of Control in implementing these measures.
Using the Hierarchy of Control
The Hierarchy of Control is a framework for identifying and implementing the most effective control measures to mitigate workplace hazards. It prioritises control methods from the most effective to the least effective:
- Elimination: Remove the hazard entirely from the workplace. This is the most effective control measure. For example, automating a process to eliminate manual handling.
- Substitution: Replace the hazard with something less dangerous. For example, using a less toxic chemical in place of a more hazardous one.
- Engineering Controls: Isolate people from the hazard. This might involve redesigning equipment or processes to minimise risk, such as installing guards on machinery.
- Administrative Controls: Change the way people work. This includes training, policies, and procedures to reduce exposure to hazards. Examples include implementing shift rotations to minimise fatigue.
- Personal Protective Equipment (PPE): Provide protective gear to employees. While essential, PPE is considered the least effective control measure because it does not eliminate the hazard itself.
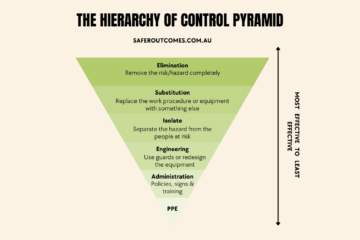
Top 10 Workplace Safety Hazards and Control Measures
1. Slips, Trips, and Falls
Hazard Explanation:
- Slips, trips, and falls are common in almost every workplace and can occur due to wet floors, uneven surfaces, clutter, or improper footwear. These incidents can result in injuries ranging from minor bruises to serious fractures and head injuries.
Control Measures:
- Housekeeping: Maintain clean and clutter-free workspaces. Regularly clean floors and remove any obstacles that could cause trips or falls.
- Signage: Use warning signs to indicate wet or slippery areas. Place signs in visible locations to alert employees and visitors.
- Flooring: Ensure floors are even and in good condition. Repair any damaged flooring promptly to prevent trips.
- Footwear: Provide employees with appropriate, non-slip footwear suitable for their working environment.
- Training: Educate employees on proper walking and climbing techniques, and encourage them to report any hazards immediately.
2. Ergonomic Injuries
Hazard Explanation:
- Poor ergonomic practices can lead to musculoskeletal disorders (MSDs), such as carpal tunnel syndrome, back pain, and tendonitis. These injuries are often caused by repetitive movements, poor posture, and improper workstation setup.
Control Measures:
- Workstation Design: Ensure workstations are ergonomically designed, with adjustable chairs, desks, and monitors that can be positioned correctly.
- Proper Posture: Train employees on maintaining proper posture while sitting or standing. Provide guidelines and reminders to promote good habits.
- Equipment: Provide ergonomic tools and equipment, such as ergonomic keyboards, mouse pads, and adjustable monitor stands.
- Breaks: Encourage regular breaks to stretch and move around. Implement policies that promote periodic breaks to reduce strain.
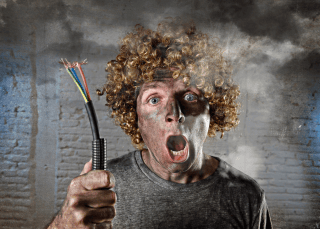
3. Electrical Hazards
Hazard Explanation:
- Electrical hazards can cause shocks, burns, and even fatalities. These hazards often arise from faulty wiring, overloaded circuits, or improper use of electrical equipment.
Control Measures:
- Regular Inspections: Conduct regular inspections of electrical systems and equipment to identify and rectify any issues.
- Maintenance: Ensure proper maintenance and repairs of electrical systems. Only qualified personnel should handle electrical repairs.
- Training: Train employees on safe electrical practices and the correct use of electrical equipment. Include information on how to recognise electrical hazards.
- PPE: Provide appropriate personal protective equipment (PPE) for electrical work, such as insulated gloves and face shields.
4. Chemical Exposures
Hazard Explanation:
- Exposure to hazardous chemicals can cause various health issues, including respiratory problems, skin irritation, and poisoning. These exposures can occur through inhalation, skin contact, or ingestion.
Control Measures:
- Proper Storage: Store chemicals in labelled, secure containers. Follow all regulations and guidelines for chemical storage.
- Ventilation: Ensure proper ventilation in areas where chemicals are used to prevent the build-up of hazardous fumes.
- Training: Train employees on handling, using, and disposing of chemicals safely. Provide information on emergency procedures in case of exposure.
- PPE: Provide necessary PPE, such as gloves, masks, and goggles, to protect against chemical exposure.
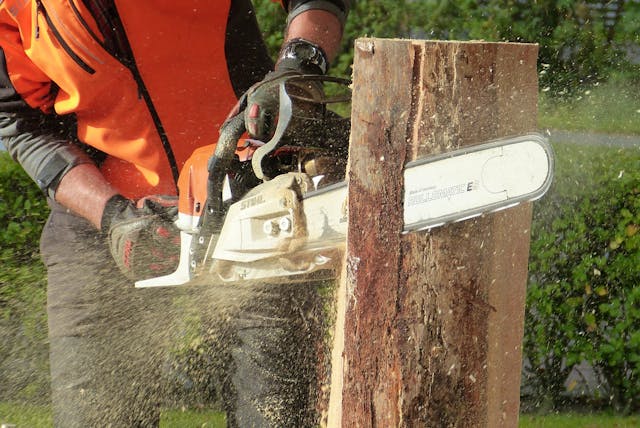
5. Machinery and Equipment Hazards
Hazard Explanation:
- Improper use or maintenance of machinery and equipment can lead to serious injuries, such as cuts, amputations, and crush injuries. These hazards are prevalent in industries such as manufacturing and construction.
Control Measures:
- Guarding: Ensure all machinery has proper guarding to protect users from moving parts. Guards should be securely in place and not easily removable.
- Lockout/Tagout: Implement lockout/tagout procedures to ensure machines are properly shut off and not started up unexpectedly during maintenance.
- Maintenance: Conduct regular maintenance and inspections of machinery to ensure they are in safe working condition.
- Training: Train employees on the safe use and maintenance of equipment. Include information on recognising potential hazards and emergency procedures.
6. Fire Hazards
Hazard Explanation:
- Fires can cause severe injuries, fatalities, and significant property damage. Common fire hazards include faulty wiring, flammable materials, and open flames.
Control Measures:
- Fire Extinguishers: Equip workplaces with adequate fire extinguishers and train employees on their use. Ensure extinguishers are regularly inspected and maintained.
- Emergency Exits: Ensure clear and accessible emergency exits. Mark exits clearly and conduct regular drills to ensure employees know evacuation routes.
- Fire Drills: Conduct regular fire drills and emergency evacuation training. Practise different scenarios to prepare for various types of fires.
- Storage: Store flammable materials safely and away from ignition sources. Follow all regulations for the storage of hazardous materials.
7. Repetitive Strain Injuries (RSIs)
Hazard Explanation:
- Repetitive strain injuries result from repetitive motions, often in office settings or assembly lines, leading to chronic pain and discomfort. These injuries can affect muscles, tendons, and nerves.
Control Measures:
- Ergonomics: Design workstations to minimise repetitive strain. Adjust workstations to fit the needs of individual employees.
- Task Variation: Rotate tasks to reduce repetitive movements. Encourage employees to vary their activities throughout the day.
- Breaks: Encourage regular breaks to rest and stretch muscles. Implement policies that promote short, frequent breaks.
- Exercises: Implement stretching and strengthening exercises as part of the daily routine. Provide guidelines on exercises that can be done at work.
8. Confined Spaces
Hazard Explanation:
- Working in confined spaces poses risks of asphyxiation, toxic exposure, and entrapment. These hazards are common in industries such as mining, construction, and utilities.
Control Measures:
- Permits: Require entry permits for confined space work. Ensure permits are issued only when all safety conditions are met.
- Monitoring: Continuously monitor the air quality in confined spaces. Use gas detectors to identify hazardous atmospheres.
- Rescue Plans: Develop and practise emergency rescue plans. Ensure rescue equipment is readily available and personnel are trained in its use.
- Training: Train employees on the specific hazards and safety procedures associated with confined spaces. Include information on emergency procedures.
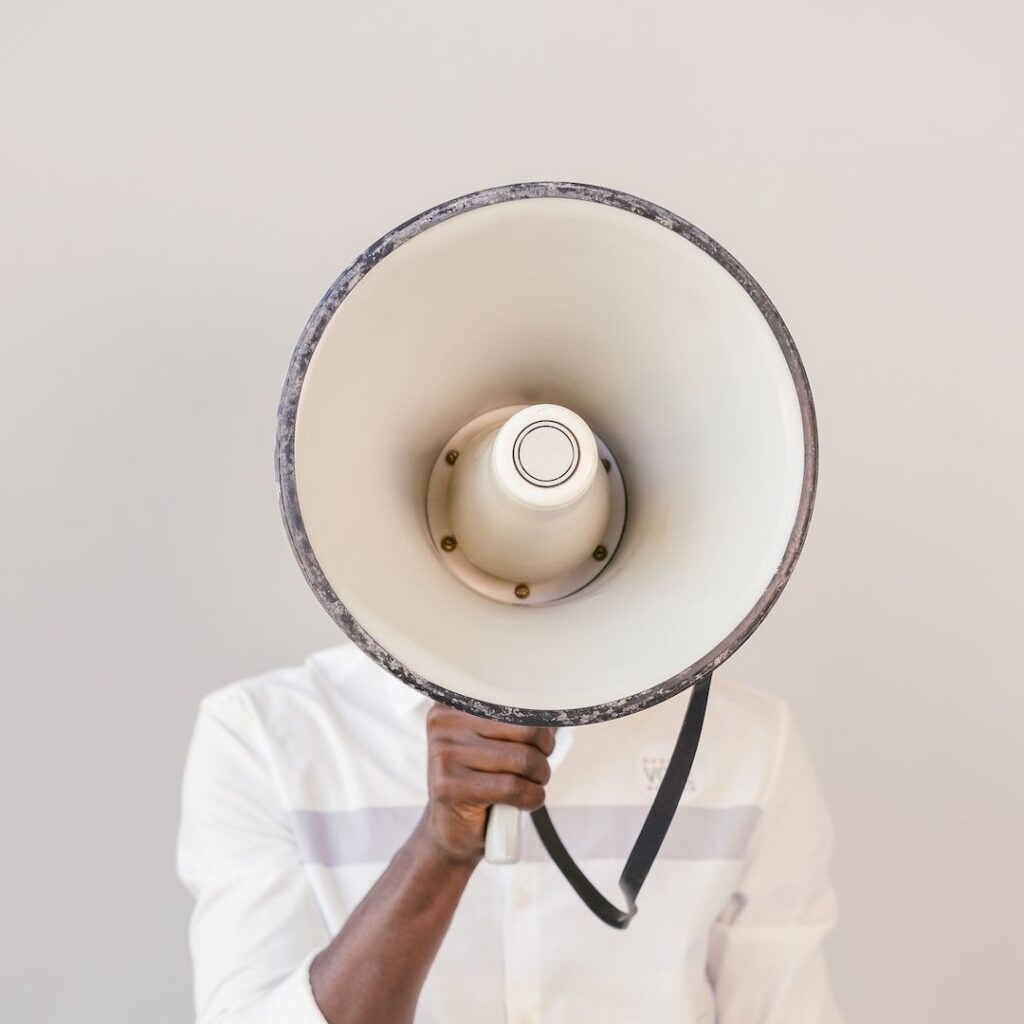
9. Noise Hazards
Hazard Explanation:
- Excessive noise levels can lead to hearing loss and other health issues, particularly in industrial and construction settings. Prolonged exposure to high noise levels can cause permanent damage.
Control Measures:
- Hearing Protection: Provide appropriate hearing protection, such as earplugs or earmuffs. Ensure employees use them correctly and consistently.
- Noise Control: Implement engineering controls to reduce noise levels, such as sound barriers and quieter machinery. Use materials and designs that absorb noise.
- Monitoring: Regularly monitor noise levels in the workplace. Use sound level meters to measure and document noise exposure.
- Hearing Tests: Conduct regular hearing tests for employees exposed to high noise levels. Monitor their hearing health and take action if changes are detected.
10. Workplace Violence
Hazard Explanation:
- Workplace violence, including physical assaults and verbal threats, can lead to injuries and psychological trauma. This hazard can occur in any industry but is more prevalent in healthcare, retail, and public service.
Control Measures:
- Policies: Develop and enforce a zero-tolerance policy for workplace violence. Clearly communicate this policy to all employees.
- Training: Train employees on recognising and de-escalating potentially violent situations. Provide techniques for managing conflict and staying safe.
- Reporting: Establish clear reporting procedures for incidents of violence. Encourage employees to report any concerns without fear of retaliation.
- Security: Implement security measures, such as surveillance cameras and controlled access. Consider hiring security personnel in high-risk areas.
General Hazards Toolbox Talk
A General Hazards Toolbox Talk is an important tool for raising awareness about various workplace safety risks and promoting a culture of safety. It involves short, focused discussions on safety topics relevant to employees’ daily tasks and work environment.
Topics Covered in a General Hazards Toolbox Talk:
- Overview of common workplace hazards.
- Specific hazards relevant to the workplace or industry.
- Recent incidents or near-misses and lessons learned.
- Updates on safety policies and procedures.
- Importance of reporting hazards and incidents.
How Often Should Toolbox Talks Be Delivered?:
- It is recommended that Toolbox Talks be held at least once a week to ensure ongoing awareness and engagement. However, the frequency can vary depending on the workplace and the specific risks involved. High-risk industries may require daily Toolbox Talks.
- Additionally, Toolbox Talks should be conducted after any significant incident, change in work procedures, or introduction of new equipment or processes to address new hazards promptly.
Conclusion
By identifying and addressing these common workplace safety hazards, organisations can create a safer work environment for their employees. Regular training, proper use of equipment, and adherence to safety protocols are essential in controlling these risks. Implementing these practical solutions will not only prevent accidents and injuries but also enhance overall productivity and employee morale. Using the Hierarchy of Control framework ensures that the most effective measures are prioritised, providing a comprehensive approach to workplace safety. Regular General Hazards Toolbox Talks further reinforce safety practices, keeping employees informed and vigilant about potential risks.
How can Safe-R Outcomes help your business?
Our Professional subscriptions contain many essential documents including:
- WHS Management Plans / Safety Manuals
- SWMS (if the job entails high risk tasks)
- a range of SOPs, Registers, Toolbox Talks, Checklists and Policies
These can all be downloaded and are not blank templates, so can be used immediately.
We also provide Induction training to help you on-board new employees and contractors.
As you can see it is all done for you so it makes it nice and simple. You can find out more on the Industries and Professions page.
If you’re concerned about the time commitment and knowledge required to implement the correct documents, procedures and training for forklift safety, Safe-R Outcomes can help. We strive to reduce the time and cost for businesses to implement their legally necessary safety requirements.