Every business should have a plan in place to test and tag as it is an important safety precaution for businesses of all sizes. This means that regular tests are conducted on all electrical equipment to ensure it is safe for use. Not only is this required by law in most instances, but it can also help to prevent fires and other accidents from occurring in your workplace.
By regularly testing your equipment for electrical faults, you can avoid dangerous and potentially costly accidents. Not only is test and tag an essential safety measure, it can also help to improve the efficiency of your workplace. Here’s what you need to know, and why it’s so important for your business.
What is test and tag?
When you are referring to test and tag, it is the process of testing all electrical equipment in a workplace for any potential dangers. This means that not only will your equipment be tested so that it is safe for use, but tagging can also give you peace of mind. Tagging is when an individual attaches a safety label to the equipment so that you can tell immediately if it is dangerous or not. The tag will also indicate when it was tested and who completed the testing.
When completing a test and tag firstly the equipment will be visually checked over for the following :
- Is the equipment in good order?
- Is the plug in good order with no fraying of the cord?
- Are there any joins or cracks in the cords insulation?
- Are there any breaks in the main lead’s insulation?
- Are all switches, controls and fuses in working order?
- Are the protective covers and guards fitted correctly?
- Does there appear to be evidence of overheating?
- Is there evidence of water damage?
- Is it in a safe condition in every other way?
After the visual inspection, the device or equipment will then be tested with an electrical device to ensure it is safe to use. A test and tag system includes tests which are designed to check that everything in a circuit is working properly. These tests are called earth loop impedance, insulation resistance, leakage current, HV insulation coordination and contact resistance.
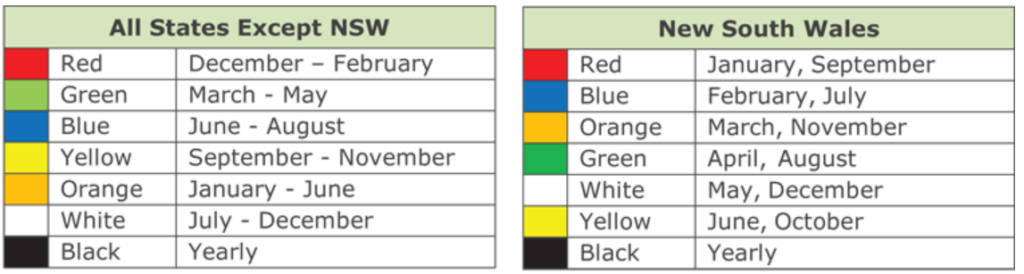
Why test and tag?
Keeping up to date with a test and tag system is important to keep your workplace safe. Test and tag systems are there to help minimise the dangers associated with electrical equipment. Test and tag ensures that all your equipment is safe to use.
Electrical equipment can be damaged without the user even being aware. Faulty electrical equipment can be caused by old wiring, loose connections, overloads of power and sub-standard components. A test and tag system ensures that you will know if there is an issue with your equipment.
Electricity is dangerous if it isn’t handled correctly. Without taking precautions, you can put yourself at risk of an injury or worse. A person can be injured by faulty electrical equipment by receiving an electric shock or by being exposed to a fire or explosion. A reminder that an electric shock isn’t just a quick zap like from static electricity, an electric shock can cause severe and long lasting injury and it can be, and is fatal.
A test and tag system helps prevent this from happening by testing the equipment for any faults so you can have it repaired or purchase new equipment. Test and tag systems will also help your employees know that your workplace complies with health and safety regulations and that you care about their safety.
Of course, other than ensuring worker safety, there are also laws in Australia in relation to test and tag. Australia is a member of the International Test and Tag federation, an organisation that has been established in various countries to ensure that their test and tag systems are up-to-date. In Australia there are two types of legislation in relation to testing and tagging:
1. Commonwealth legislation which requires electrical equipment to be maintained safely, including providing information on how this equipment can be maintained safely.
2. State and territory legislation which requires electrical equipment to be certified as safe to use in the workplace
Test and tagging is a requirement for your business as it ensures that all your electrical equipment complies with Australia’s health and safety legislation.
Some industries have mandatory test and tag such as construction, while others while not mandated are expected due to employers having a duty of care to workers.
Is test and tag a legal requirement?
As discussed previously, in certain industries the government has implemented mandatory test and tag requirements. This is because they are seen as having a higher risk of incidents occuring due to the nature of their work and the tools and equipment they use. Using construction as an example, all tools and equipment needs to be tested and tagged every three (3) months. This is a legal requirement as construction is seen as a high risk industry.
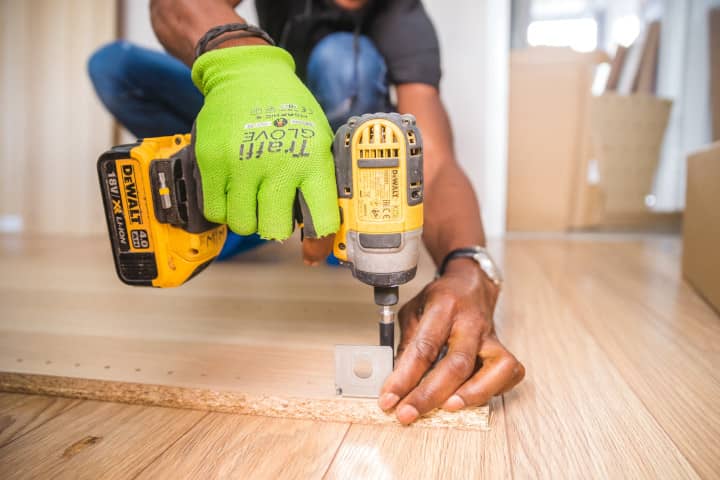
On the other hand, not all industries are mandated with mandatory test and tag requirements. However, even though they aren’t legally required, employers still have a duty of care to their employees. So it is generally accepted that you should test and tag equipment in your workplace if you are an employer with a duty of care to your employees.
If you choose not test and tag your equipment, you could leave yourself open to legal action if something were to happen as a result of faulty equipment. If this is the case, any injury or damage that occurs due to faulty equipment may be legally attributed back to you as the employer. And you should also consider whether your insurance company will pay out if you have not done everything you can to reduce the risk of an incident occuring.
Who can do test and tag?
Many people think that only an electrician can conduct test and tags, however trained technicians can also complete the task.
Test and tag does involve working with electricity, so if your employees aren’t trained to work with it then often this is done by an electrician or other qualified technicians. There are strict codes for testing and tagging equipment in Australia, so you wouldn’t want to go about it incorrectly.
The legislation states that the person must be competent to complete the task, often this means that if they are not an electrician they have completed an accredited test and tag course. In some states, for instance Queensland, the technician is also required to obtain a licence if they are completing test and tag for anyone other than themselves.
What is a test and tag register?
A test and tag register allows you to see in one place all your testing and tagging information. The test and tag register is a great record of what was tested, when it was tested, who tested it and whether or not the testing met the required standard. It also should list all the equipment that has been tagged as well as which type of tags have been used.
The register needs to be kept for a minimum of five years, however the more time you keep it for the better. It will serve as a reminder that all your equipment has been tested and tagged in accordance with the law, if an inspection was to be conducted of your workplace, or even worse an incident that required you to hand over all your safety documentation to police or lawyers.
Where can I get a test and tag register?
In short, whether you work in an industry that requires regular test and tag, or you own a business where it is not mandated by law, it is generally accepted that testing and tagging your tools and equipment is the responsible thing to do. Not only does it ensure you are legally compliant, but also reduces the risk of injury to workers using them.
So if you own a business or work in an industry where test and tag isn’t mandated by law take the initiative in meeting your duty of care, and test and tag your equipment to ensure you are following the law.
Test and Tag Toolbox Talk
Not many companies will do a test and tag toolbox talk, however we believe it is a relevant and useful toolbox talk especially in the construction industry.
The aim of the toolbox talk is to ensure that all workers are aware of the importance of testing and tagging, as well as what needs to be done in order to comply with the law. It is also an opportunity to reinforce the importance of safety in the workplace, and how each worker can play a role in ensuring the safety of themselves and their colleagues
How often should a test and tag toolbox talk be given?
There is no legislation that states how often a test and tag toolbox talk should be given, however we recommend delivering one at least once a year or at the beginning of a new project that has new workers or contractors. This will ensure that all workers are up to date with the latest test and tag requirements, as well as providing a refresher on the importance of safety in the workplace. It could also be given in the event that an incident occurs due to lack of test and tag , as a way to remind workers of the importance of compliance.
How can Safe-R Outcomes help your business?
Our Professional subscriptions contain many essential documents including:
- WHS Management Plans / Safety Manuals
- SWMS (if the job entails high risk tasks)
- a range of SOPs, Registers, Toolbox Talks, Checklists and Policies
These can all be downloaded and are not blank templates, so can be used immediately.
We also provide Induction training to help you on-board new employees and contractors.
As you can see it is all done for you so it makes it nice and simple. You can find out more on the Industries and Professions page.
If you’re concerned about the time commitment and knowledge required to implement the correct documents, procedures and training for forklift safety, Safe-R Outcomes can help. We strive to reduce the time and cost for businesses to implement their legally necessary safety requirements.