No matter what your trade is, most workers in construction at some time work at height, or nearby to where others are working at height. Safe work method statements help everyone who is working on site to understand what their responsibilities are, and how they can work safely. Conducting tool box talks focusing on the risks of working at heights is another way to ensure everyone is aware what is going and also meets the legal requirement to consult and communicate with workers.
What does working at height mean?
There is some confusion over the term ‘working at height’ and what it means in a practical sense. On a construction site work where you can fall over 2 metres is considered a high risk activity and requires a safe work method statement. However any work that is conducted anywhere above solid ground is working at height. So whether you’re working on a step ladder or on a scissor lift you have to manage the risk of falls of people, equipment and materials. This can be further complicated by state by state rules about when certain control measures are required for instance in some states there are different rules for commercial and residential contruction work regarding the height at which these measures come into play.
What are the risks of working at height?
Working at height is one of the most common causes of worker injuries and fatalities. The risks associated with working at heights include:
- Falls from an elevation;
- Falls to a lower level;
- Being struck by falling objects or equipment;
- Slipping and falling into uncovered excavations
Work at heights can be particularly hazardous because of the combination of higher elevation, slippery and cluttered work surfaces, and restricted footing or maneuvering room. Even if fall protection is provided as part of a guardrail system or personal fall arrest system, these systems cannot fully protect workers from falling. They do not prevent workers from stepping into a hole or off the edge of a surface, and they do not guarantee that a worker will be clear of all falling objects and debris.
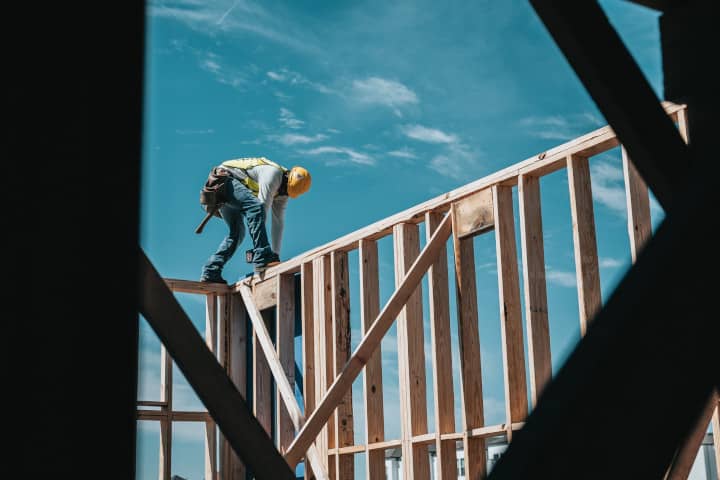
How can employers ensure their employees work at height safely?
Employers should assess the workplace for hazards, such as:
- unguarded holes, edges, ledges, and other openings in the floor or ground;
- ladders over open holes or equipment with moving parts;
- slippery or cluttered surfaces;
- loose handrails on stairs and ladders;
- protruding nails, screws, and other fasteners;
- overhead electrical lines;
- improperly stacked materials that may collapse;
- and any other situations where a fall hazard exists.
Employers should set up guardrail systems and other protection such as screens, netting or scaffolding to protect workers from falls on surfaces where the height is more than 2 metres in commercial construction and 3 metres in residential construction.
Working at height control measures
There are many types of PPE and equipment that workers can use and wear to help reduce the risk of injury or death when working at height. If we look at the hierarchy of control we can see the best option is to completely remove the task of having to work at height, but unfortunately in many cases that is just not able to be done. The work still needs to be done, but just as safely as possible. So here are some controls measures to help keep workers safe when working at height.
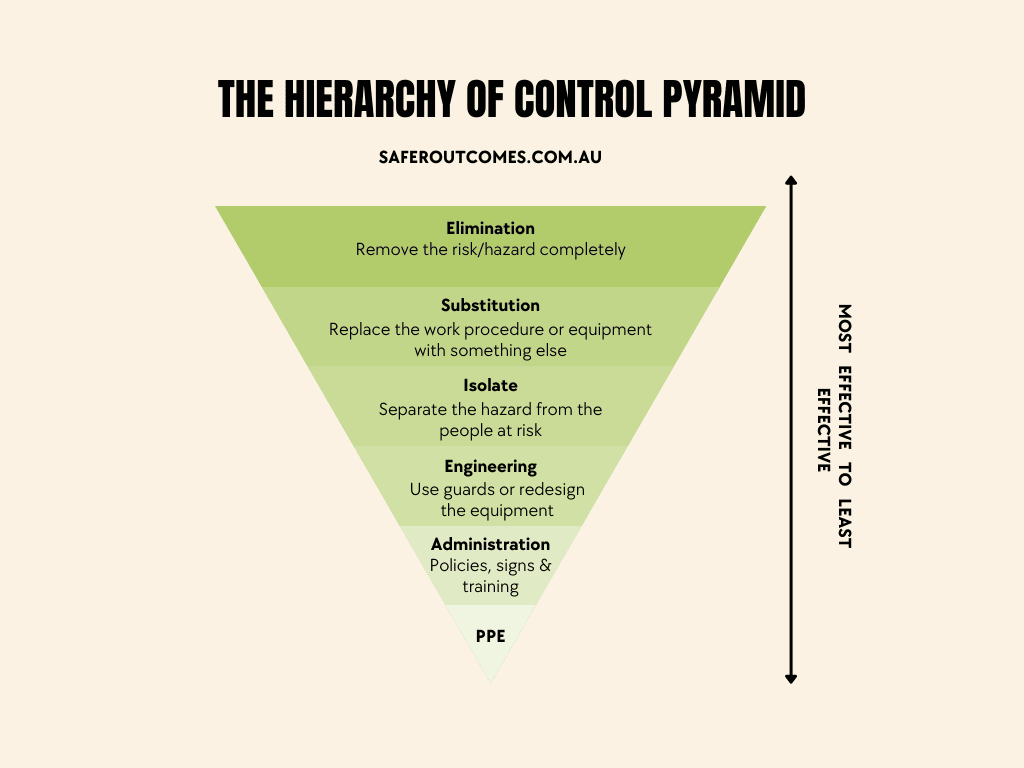
- Training – ensuring that the worker has the right training and information to be able to complete their task safely;
- Substitution – removing the need to work at height, if this isn’t possible finding a safer way of doing the same task;
- Engineering controls (mitigations) – selecting and using equipment and devices such as: scaffolds, work platforms, guardrails, safety nets, fall arrest systems or harnesses;
- Administrative controls (mitigations) – using safe work procedures or policies, for example a working at height safe work method statement
- Personal protective equipment (PPE) – providing the right PPE for the task, including safety harnesses and lanyards.
Just because you are an employee of a company does not mean you cannot be held personally responsible if you do not follow the work at height procedures or rules that are in your job description.
Employer working at height requirements
Employers must train each employee who works at height about the specific hazards of their job and what can be done to help them avoid injury, illness, and death while they work.
Working at height training in the workplace is different from a formal and nationally recognised working at height training course.
This includes reviewing each task and calculating the risks of working at height. Employers should be sure to:
- Train workers fully in the proper procedures for installing, maintaining, and using any equipment or tools they will use as part of their work;
- Ensure that all employees understand what personal protective equipment (PPE) must be used to prevent injury from falls;
- Instruct workers to inspect all equipment before use and take it out of service if it is defective, damaged, or dropped;
- Check PPE each time it is used to ensure that nothing has happened to damage or reduce its effectiveness; and
- Ensure that employees keep aisles clear of tools and materials to permit safe passage through the workplace;
- Provide proper training for employees who are required to work from heights;
- Ensure that workers are familiar with the rules of their employer’s workplace, which must include the appropriate procedures for working safely at height;
- Provide all equipment and tools needed for the job, including fall protection equipment if required;
- Ensure that employees follow established safe methods of working at height. In addition, workers should be encouraged to report unsafe working conditions so they can be corrected before an accident happens; and
- Develop a system of regular inspections to find hazards and correct them before an accident happens.
Employees must feel comfortable in reporting on the hazards they are exposed to at work, even if it means that their employer will be required to provide safer working conditions for them. If employees are not on board with these ideas or do not report any dangers then employers have a hard time correcting these dangerous problems and protecting their employees.
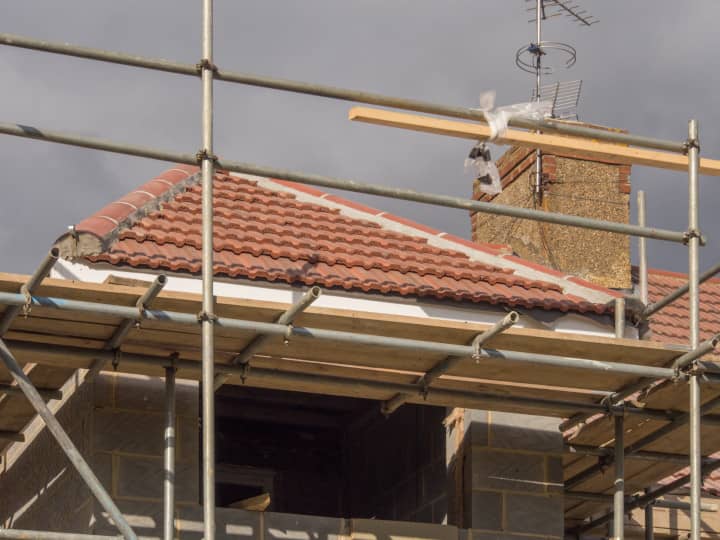
Working at Height Safe Work Method Statement
In Australia, if you are completing construction work at a height over two metres you need a safe work method statement (SWMS) for the task. An SWMS is a written plan that outlines all the steps an employer will take to reduce risks for any task occurring at height. For example, if you are working on top of a ladder then your SWMS must include details about how you will access and leave the work area safely, what kind of fall protection equipment you will use (if required), and who is required to be involved with the task. If you want help to write your own SWMS using a free template please read What are SWMS and how do I write one using a free template?
A safe work method statement can be completed for the entire job or trade, it doesn’t need to be just a ‘working at height SWMS’. And, you can have a SWMS in place even if the work isn’t being completed at a height of over two metres, this ensures your workers are aware of their safety obligations and you are also meeting your legislative requirements as a business owner.
Employers must ensure that a SWMS is in place before workers start any work at height over 2 metres and the employee must acknowledge the SWMS when it is issued. Employers should make sure to also have an emergency action plan in place, which includes what will happen if someone fell from a height and was injured as a result.
Working at height is one of the most common causes of fatalities and major injuries in Australia, so it is important for everyone to follow these guidelines and stay safe on the job. Ladder Safety – Don’t Fall for Misinformation can also help with tips and advice you might not be aware of.
Your safe work method statement will for the most part include everything we’ve discussed previously, which can make it easier for you to write your own.
Working at height toolbox talk
Giving a working at height toolbox talk is an important and simple technique to instruct your workers in working at height. It only takes a few minutes and ensures that the knowledge is fresh in everyone’s mind.
The toolbox talk should be taken seriously by all employees. You can prevent injuries and improve the culture of your workplace by making working at height toolbox talks at least a little bit appealing. Ask questions like “What is the most common workplace injury from ladders?” or “Who can tell me how to use a ladder safely?” to make it more engaging.
How often do I need to give a toolbox talk about working at height?
Before starting a new project or when your staff have changed, you should do a working at height toolbox talk. It is a crucial part of keeping your workplace safe, and it has the potential to save lives. Toolbox talks also improve the safety culture within the business which can have other positive effects on moral and general workplace behaviours.
How can Safe-R Outcomes help your business?
Our Professional subscriptions contain many essential documents including:
- WHS Management Plans / Safety Manuals
- SWMS (if the job entails high risk tasks)
- a range of SOPs, Registers, Toolbox Talks, Checklists and Policies
These can all be downloaded and are not blank templates, so can be used immediately.
We also provide Induction training to help you on-board new employees and contractors.
As you can see it is all done for you so it makes it nice and simple. You can find out more on the Industries and Professions page.
If you’re concerned about the time commitment and knowledge required to implement the correct documents, procedures and training for forklift safety, Safe-R Outcomes can help. We strive to reduce the time and cost for businesses to implement their legally necessary safety requirements.