Safety audits are essential for maintaining and enhancing workplace safety standards. By systematically examining safety practices, procedures, and compliance with regulations, organisations can identify areas for improvement and prevent potential accidents. This article delves into what a safety audit is, who should conduct it, the importance of regular safety audits, how to conduct a thorough safety audit, and how to use audit results to drive continuous improvement.
What is a Safety Audit?
A safety audit is a systematic evaluation of an organisation’s safety practices, procedures, and compliance with relevant regulations and standards. The primary goal is to identify potential hazards, assess the effectiveness of existing safety measures, and recommend improvements to enhance workplace safety. Safety audits can cover various aspects, including physical conditions, equipment, employee behaviour, and administrative controls.

Who Should Conduct a Safety Audit?
- Internal Auditors:
- Safety Officers: Trained safety officers within the organisation are often responsible for conducting internal safety audits. They are familiar with the company’s operations and safety policies.
- Safety Committees: A group of employees representing different departments can collaborate to conduct comprehensive safety audits, bringing diverse perspectives and expertise.
- External Auditors:
- Consultants: Professional safety consultants or firms can provide an unbiased and thorough evaluation of the organisation’s safety practices. They bring expertise from various industries and can offer fresh insights.
- Regulatory Agencies: Government or regulatory bodies may conduct safety audits to ensure compliance with legal requirements and standards.
- Combined Approach:
- Hybrid Teams: Combining internal and external auditors can leverage internal knowledge and external expertise, providing a more comprehensive and balanced safety audit.
Importance of Regular Safety Audits
- Identifying Hazards:
- Early Detection: Regular safety audits help in identifying both existing and potential hazards in the workplace. By recognising these risks early, organisations can take corrective actions before they lead to accidents or injuries.
- Comprehensive Risk Assessment: Audits ensure a thorough examination of all aspects of the workplace, from physical hazards to procedural weaknesses, thus providing a holistic view of the safety environment.
- Ensuring Compliance:
- Legal Obligations: Safety audits ensure that the workplace complies with relevant safety regulations and standards, helping avoid legal penalties and fines.
- Internal Policies: They also verify adherence to internal safety policies, ensuring that all organisational safety protocols are being followed correctly.
- Promoting a Safety Culture:
- Employee Engagement: Regular audits demonstrate a commitment to safety, encouraging employees to prioritise and engage in safe practices.
- Continuous Improvement: By constantly evaluating and improving safety practices, organisations foster a culture of continuous improvement and vigilance.
- Reducing Costs:
- Preventing Accidents: By identifying and mitigating risks, safety audits can prevent costly accidents and injuries.
- Insurance Premiums: Maintaining a safe work environment can also lead to lower insurance premiums, as it demonstrates proactive risk management.
- Enhancing Employee Morale:
- Safe Environment: A safe working environment boosts employee morale and productivity. When employees feel safe, they are more likely to be engaged and motivated.
- Trust in Management: Regular audits show that management cares about employee well-being, building trust and loyalty among the workforce.
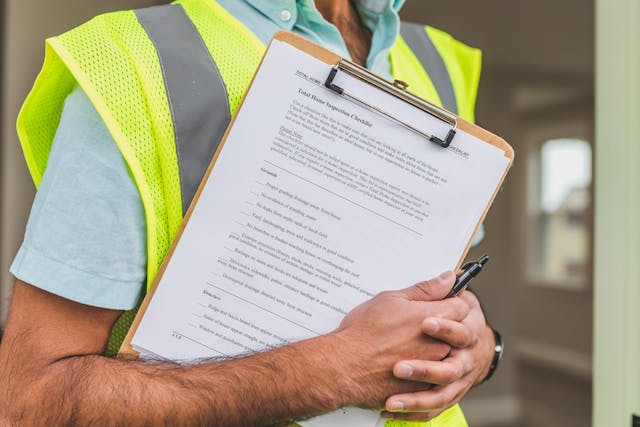
How to Conduct a Thorough Safety Audit
- Plan the Audit:
- Define Scope and Objectives: Clearly outline what the audit will cover and the goals you aim to achieve. This could include specific areas, departments, or processes.
- Customised Checklists: Develop customised checklists based on the specific requirements of different areas or departments.
- Select the Audit Team: Choose qualified personnel to conduct the audit, including safety professionals and representatives from relevant departments.
- Define Scope and Objectives: Clearly outline what the audit will cover and the goals you aim to achieve. This could include specific areas, departments, or processes.
- Gather and Review Documentation:
- Review Safety Policies: Examine existing safety policies, procedures, and records. This includes incident reports, previous audit findings, training records, and maintenance logs.
- Historical Data: Analyse historical data to identify trends and recurring issues.
- Compliance Records: Check compliance with state safety regulations.
- Regulatory Updates: Stay informed about recent changes in safety regulations to ensure the audit reflects current requirements.
- Review Safety Policies: Examine existing safety policies, procedures, and records. This includes incident reports, previous audit findings, training records, and maintenance logs.
- Conduct On-site Inspections:
- Visual Inspections: Walk through the workplace to observe practices, equipment, and working conditions. Take note of any hazards, unsafe behaviours, or non-compliance issues.
- Detailed Observations: Use detailed observation checklists to ensure no aspect is overlooked.
- Interviews and Observations: Speak with employees and observe their tasks to understand safety practices and identify areas for improvement.
- Employee Feedback: Gather feedback from employees about potential hazards and safety concerns.
- Visual Inspections: Walk through the workplace to observe practices, equipment, and working conditions. Take note of any hazards, unsafe behaviours, or non-compliance issues.
- Identify and Document Findings:
- Record Hazards and Issues: Document all identified hazards, non-compliance issues, and areas needing improvement. Use photographs and detailed descriptions for clarity.
- Severity Ratings: Assign severity ratings to each identified hazard to prioritise corrective actions.
- Risk Assessment: Evaluate the severity and likelihood of identified risks. Prioritise issues based on their potential impact on safety.
- Risk Matrix: Use a risk matrix to visually represent the severity and likelihood of risks.
- Record Hazards and Issues: Document all identified hazards, non-compliance issues, and areas needing improvement. Use photographs and detailed descriptions for clarity.
- Develop an Action Plan:
- Recommend Corrective Actions: Suggest practical and effective measures to address identified issues. This could include changes in procedures, additional training, or equipment upgrades.
- SMART Goals: Set Specific, Measurable, Achievable, Relevant, and Time-bound (SMART) goals for corrective actions.
- Assign Responsibilities: Clearly assign responsibilities for implementing corrective actions and set deadlines for completion.
- Accountability Framework: Establish an accountability framework to track progress and ensure completion of actions.
- Recommend Corrective Actions: Suggest practical and effective measures to address identified issues. This could include changes in procedures, additional training, or equipment upgrades.
- Report and Communicate Findings:
- Detailed Audit Report: Prepare a comprehensive report summarising findings, risks, and recommended actions. Include a timeline for follow-up and re-evaluation.
- Executive Summary: Provide an executive summary for senior management highlighting key findings and recommendations.
- Communicate with Stakeholders: Share the audit results with management, safety committees, and employees. Ensure everyone understands the findings and their role in addressing them.
- Transparent Communication: Maintain transparency in communication to build trust and ensure collective responsibility.
- Detailed Audit Report: Prepare a comprehensive report summarising findings, risks, and recommended actions. Include a timeline for follow-up and re-evaluation.
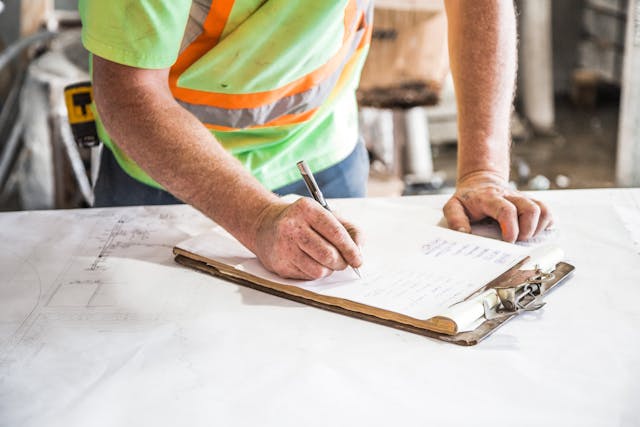
Using Audit Results to Drive Continuous Improvement
- Implement Corrective Actions:
- Follow Through: Ensure that the recommended corrective actions are implemented promptly. Monitor progress and provide support as needed.
- Implementation Timeline: Set clear timelines for the implementation of corrective actions.
- Update Procedures: Revise safety policies and procedures based on audit findings. Ensure that changes are communicated to all employees.
- Policy Revisions: Regularly review and update safety policies to reflect new insights and best practices.
- Follow Through: Ensure that the recommended corrective actions are implemented promptly. Monitor progress and provide support as needed.
- Track and Measure Progress:
- Regular Monitoring: Continuously monitor the implementation of corrective actions and their effectiveness. Use key performance indicators (KPIs) to measure improvements.
- Performance Metrics: Develop metrics to evaluate the impact of safety improvements.
- Periodic Reviews: Conduct follow-up audits to verify that corrective actions have been effective and to identify any new issues.
- Audit Cycle: Establish a regular audit cycle to ensure ongoing evaluation and improvement.
- Regular Monitoring: Continuously monitor the implementation of corrective actions and their effectiveness. Use key performance indicators (KPIs) to measure improvements.
- Foster a Culture of Continuous Improvement:
- Engage Employees: Encourage employees to participate in safety audits and provide feedback on safety practices. This helps in identifying areas for improvement and promotes a culture of continuous learning.
- Employee Involvement: Involve employees in safety committees and improvement initiatives.
- Training and Education: Regularly update training programs to reflect new safety practices and audit findings. Ensure that employees are aware of the latest safety procedures and standards.
- Ongoing Training: Provide continuous learning opportunities to keep employees informed about safety advancements.
- Engage Employees: Encourage employees to participate in safety audits and provide feedback on safety practices. This helps in identifying areas for improvement and promotes a culture of continuous learning.
- Leverage Technology:
- Use Audit Software: Implement audit management software to streamline the audit process, track findings, and ensure timely implementation of corrective actions.
- Digital Tools: Utilise digital tools to enhance data collection, analysis, and reporting.
- Data Analytics: Utilise data analytics to identify trends, predict potential risks, and develop targeted safety interventions.
- Predictive Analysis: Employ predictive analytics to anticipate and mitigate future risks.
- Use Audit Software: Implement audit management software to streamline the audit process, track findings, and ensure timely implementation of corrective actions.
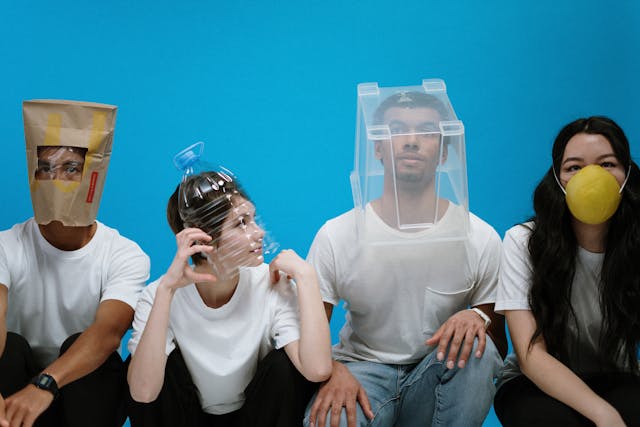
Conclusion
Regular safety audits are essential for maintaining a safe working environment and driving continuous improvement. By systematically identifying hazards, ensuring compliance, and fostering a culture of safety, organisations can prevent accidents, reduce costs, and enhance employee morale. Conducting thorough safety audits and effectively using the results to implement corrective actions and track progress is key to achieving these goals. With a commitment to ongoing improvement, organisations can ensure a safer, more productive workplace for all employees.
How can Safe-R Outcomes help your business?
Our Professional subscriptions contain many essential documents including:
- WHS Management Plans / Safety Manuals
- SWMS (if the job entails high risk tasks)
- a range of SOPs, Registers, Toolbox Talks, Checklists and Policies
These can all be downloaded and are not blank templates, so can be used immediately.
We also provide Induction training to help you on-board new employees and contractors.
As you can see it is all done for you so it makes it nice and simple. You can find out more on the Industries and Professions page.
If you’re concerned about the time commitment and knowledge required to implement the correct documents, procedures and training for forklift safety, Safe-R Outcomes can help. We strive to reduce the time and cost for businesses to implement their legally necessary safety requirements.