As a business owner, you likely have a good idea of what it takes to keep your business running safely. But do you have a safe operating procedure in place? Safe operating procedures can seem like overkill for some businesses, but they are an essential part of keeping your employees and customers safe. In this blog post, we’ll discuss what a safe operating procedure is and why your business might need one. We’ll also provide tips for creating your own safe operating procedure. Read on to learn more!
What is a safe operating procedure?
A safe operating procedure, sometimes called an SOP, is a set of detailed instructions that outlines how to safely perform a task or activity, or use a piece of equipment or a tool. Safe operating procedures are usually specific to a certain type of equipment or process, and they often need to be followed to the letter in order to avoid accidents or injuries.
What is the difference between a safe operating procedure and a standard operating procedure?
The main difference between a safe operating procedure and a standard operating procedure is that an safe operating procedure must be followed in order to avoid potential hazards, while a standard operating procedure is simply a set of best practices that can help improve efficiency or quality.
Standard operating procedures are not always mandatory, but safe operating procedures usually are. Standard operating procedures also tend to be less specific than safe operating procedures, since they don’t need to account for every potential hazard. A safe operating procedure may even include the standard operating procedures for tools and equipment that will be used during the task.
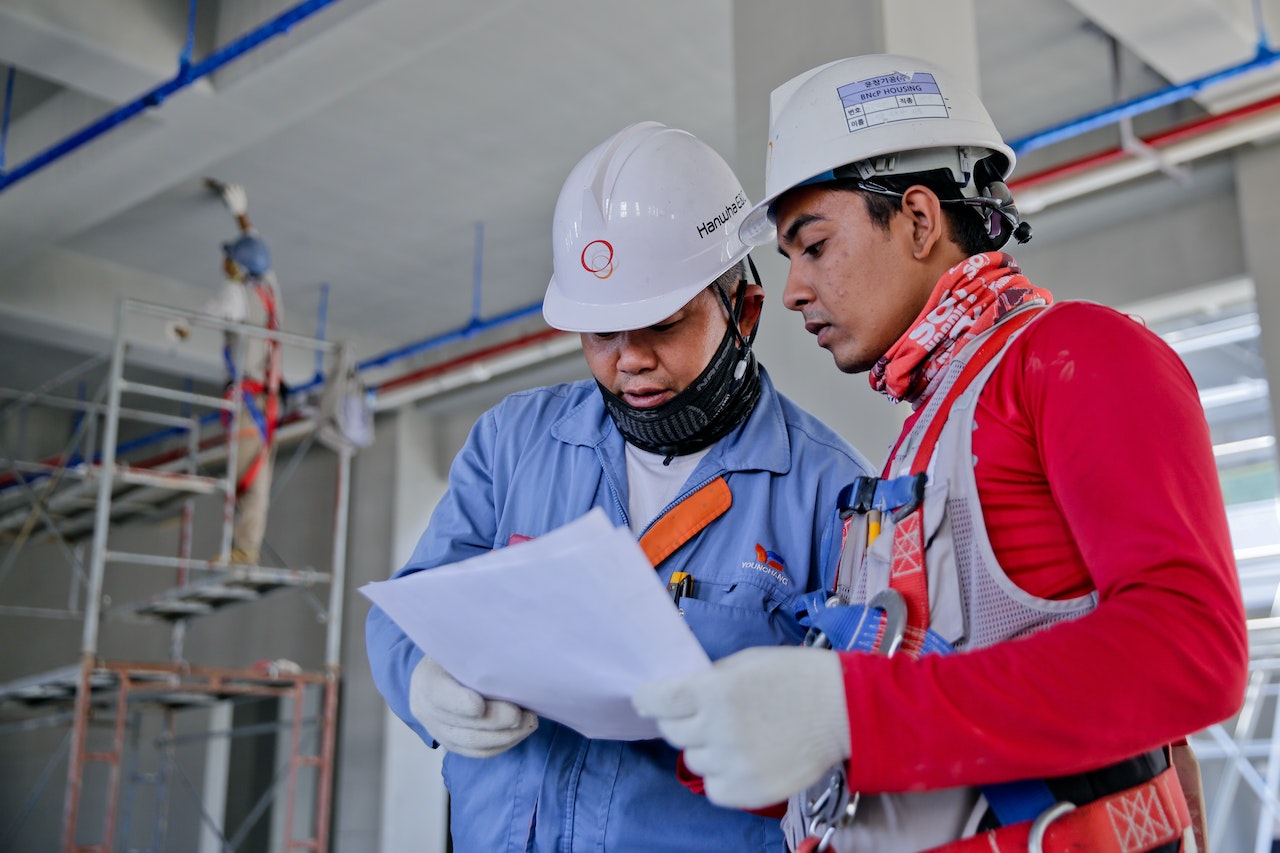
What is the difference between a safe operating procedure and a job safety analysis?
A job safety analysis (JSA) is similar to a safe operating procedure in that it is a detailed set of instructions for doing something safely. However, JSAs are typically used for more complex or dangerous tasks, and may just be for specific tasks within a larger job. For example, a mechanic may have a JSA for working in and around a workshop pit, but have a safe operating procedure for using a particular power tool.
What is the difference between a safe operating procedure and a safe work method statement?
A safe work method statement (SWMS) is a type of risk assessment where a whole job is broken down into tasks, then all the hazards and risks are identified, and the controls that will be used identified. For some types of work SWMS are required by legislation. You can find out more about safe work method statements here. While as mentioned, a SOP is a set of detailed instructions for a task or a piece of equipment or a tool, an SWMS is more like a plan.
Why do businesses need safe operating procedures?
There are many reasons why businesses need safe operating procedures. First and foremost, they help to keep employees safe. If your employees know exactly what they need to do in order to safely perform a task, they’re less likely to get hurt while doing it. Additionally, well-written safe operating procedures can help to prevent accidents and injuries by providing clear instructions on how to avoid potential hazards.
Another reason why businesses need safe operating procedures is that they can help to improve efficiency. When everyone knows exactly what they need to do in order to complete a task safely, the task can be completed more quickly and without any errors. This is especially important in businesses that rely on machinery or other equipment to get the job done – if something goes wrong with the equipment, having a safe operating procedure in place can help to prevent further damage and downtime.
Finally, businesses need safe operating procedures because they’re often required by law even if they aren’t specifically noted. For instance, in Australia business owners have a duty of care to their employees to ensure that they are provided with a safe working environment. This means that businesses need to have systems and procedures in place to minimise the risks of injury or illness in the workplace. Having safe operating procedures is one way to meet this legal obligation. And by having it in writing you can provide the much needed evidence to inspectors, regulators or lawyers if something does go wrong.
How do I choose what jobs or equipment require a safe operating procedure?
The first step is to identify the potential hazards associated with the job or equipment. Once you know what the hazards are, you can decide whether a safe operating procedure is necessary to control the risks. In some cases, the hazard may be low enough that a standard operating procedure will suffice. However, if there is a chance of serious injury or death, then a safe operating procedure is likely to be required.
The next step is to determine who will be using the equipment or performing the job. If it’s just you, then you may be able to get away with a less formal document such as a set of written instructions. However, if other people will be using the equipment or performing the job, then it’s important to make sure that the safe operating procedure is clear and easy to follow. The last thing you want is for someone to get hurt because they didn’t understand the instructions.
You should also consider the formal training of the people doing the work, if they have qualifications as a baker for instance, unless there is something special about the equipment a safe operating procedure may not be needed. However, if they are a trainee or just a general helper using the same equipment a safe operating procedure (and training) may be needed.
Finally, you need to decide how detailed the safe operating procedure needs to be. This will depend on the complexity of the task and the experience of the people who will be performing it. For example, if you’re just using a power drill to put some holes in a piece of wood, then a few simple instructions will suffice. However, if you’re operating a large piece of machinery, then the safe operating procedure will need to be much more detailed.
What should be included in a safe operating procedure?
Now that we’ve answered the question “what is a safe operating procedure?”, let’s take a look at what should be included in one. Here are some of the key elements that every safe operating procedure should have:
- A clear description of the task or activity that is to be carried out or the tool or equipment that is being used
- A step-by-step guide on how to safely use the tools or equipment, or carry out the task or activity
- A list of any hazards that could be encountered while using the tools or equipment, or carrying out the task or activity and how to avoid them
- A list of any safety equipment or PPE that is required for tools or equipment, or the task or activity
- The name and contact details of the person responsible for overseeing the safe completion of the task or activity
When creating a safe operating procedure, it’s important to make sure that it is clear and concise. The last thing you want is for your employees to be confused about what they need to do or how they need to do it. If possible, it’s also a good idea to include illustrations or photos along with the written instructions. This can help to make the safe operating procedure even easier to understand and follow.
If you’re not sure where to start, there are plenty of templates and examples of safe operating procedures available online.
Alternatively, you could hire a professional to create a safe operating procedure for you.
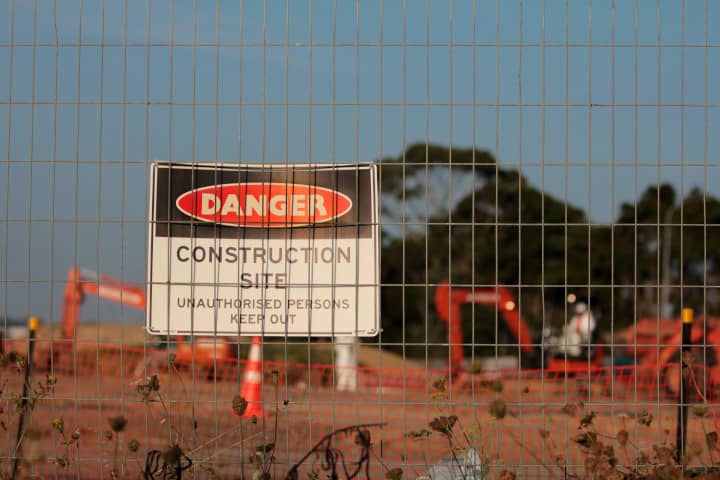
Consultation for Safe Operating Procedures
In all states of Australia the legislation says you need to consult with workers about safety matters that may affect them in the course of their work, including the introduction of new Safe Operating Procedures (SOPs). You also need to consult about changes to SOPs that may affect workers’ safety.
Consultation provides an opportunity for workers and others (e.g. health and safety representatives) to raise concerns about hazard identification, risk assessment and control measures related to the work and to participate in decisions about how the work will be carried out safely.
Consultation should include:
- discussion about hazard identification, risk assessment and control measures related to the work;
- information sharing about SOPs that are proposed or being developed;
- discussion about the SOPs and how they will be implemented;
- opportunities for employees and others to have a say about the SOPs; and
- agreement on how the SOPs will be implemented.
Consultation with workers is a really easy way to help you meet your safety obligations.
Safe Operating Procedure Training
Once you’ve created your safe operating procedure, it’s important to make sure that everyone who needs to use it is properly trained. This will help to ensure that they understand the procedures and know how to safely carry out the task or activity.
If possible, it’s a good idea to provide formal training on safe operating procedures. This could be in the form of a classroom-based training course or an online video tutorial.
In some cases, it may also be necessary to provide on-the-job training. This is where someone who is already experienced in carrying out the task or activity shows the new employee how to do it safely.
Once the employee has been trained, it’s important to make sure that they are competent in carrying out the task or activity safely. This could involve them completing a test or assessment to prove their knowledge.
It’s also a good idea to regularly review the safe operating procedure to make sure that it is still up-to-date and relevant. This is especially important if any changes have been made to the way in which the task or activity is carried out.
Safe Operating Procedure Toolbox Talk
A toolbox talk is a short, informal safety meeting that is typically held on-site. They are often used to discuss specific safety issues or risks that have been identified.
Toolbox talks can be an effective way to raise awareness of safe operating procedures in general and make sure that everyone is aware that they are used within the business and that they need to be followed.
You could also use a specific safe operating procedure as the basis for a toolbox talk, it’s a great way to make sure that everyone knows about the procedure and understands how to carry it out safely.
When delivering a toolbox talk , it’s important to:
- keep it short and focused;
- make sure that everyone understands the message;
- encourage questions and discussion; and
- follow up after the meeting if any issues or questions have been raised
Safe Operating Procedure Resources
There are lots of resources available to help you create and implement safe operating procedures within your business. Here are just a couple that you might find useful:
- Safety Management Systems: A Guide for Business – This guide from SafeWork Australia provides information on how to develop and implement a safety management system, including safe operating procedures.
- Creating Safe Work Procedures – This fact-sheet from WorkSafe Victoria provides information on what needs to be included in a safe work procedure and how to go about creating one.
You could also get further information from your state regulator or if you are a member of an industry body, they may also have resources for you.
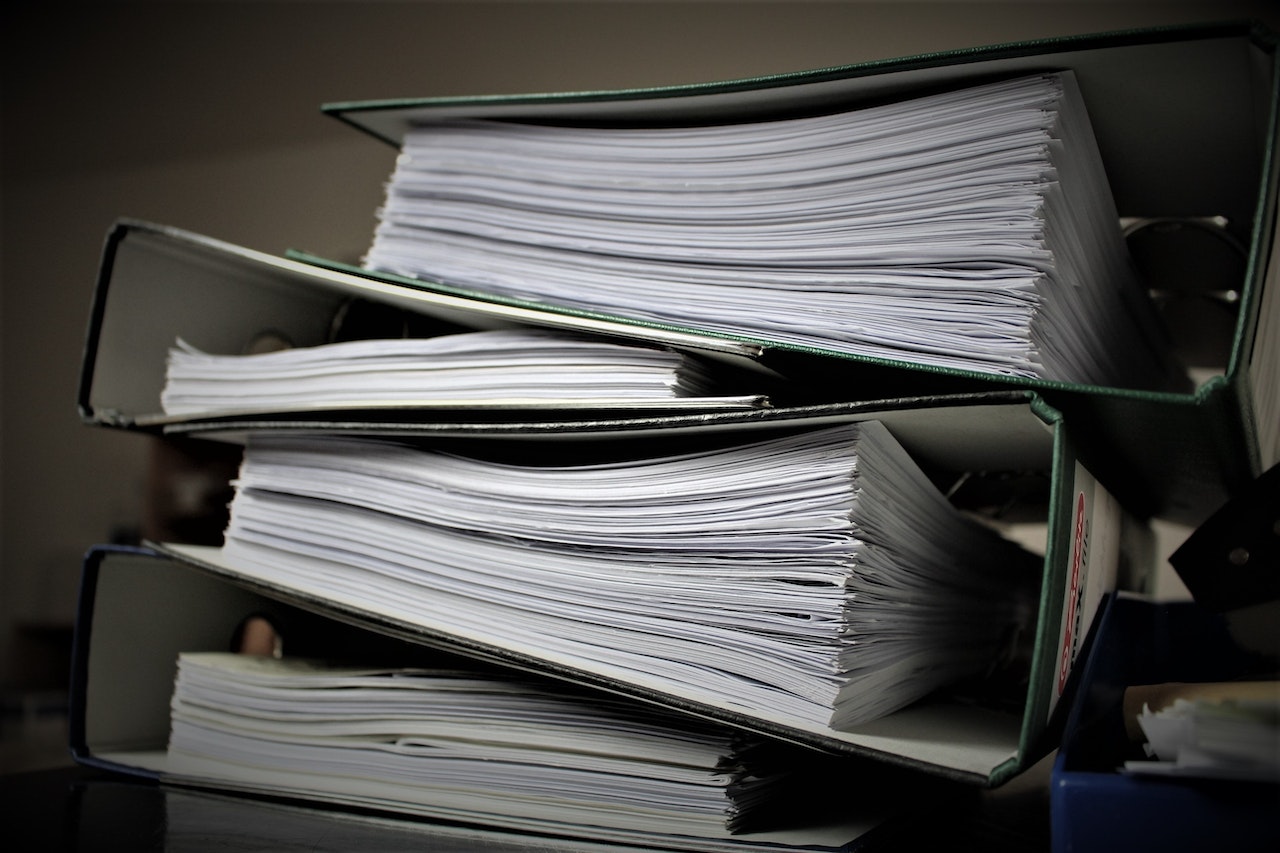
How can Safe-R Outcomes help your business?
Safe-R Outcomes has an ever growing library of safe operating procedures that mean you don’t have to worry about writing them yourself.
We offer an annual subscription service which gives you unlimited access to all of our procedures and other safety documents for one low price. This is a great option for businesses who regularly need to carry out new or different tasks and want to ensure everything is up to date with legislation.
And if we don’t have the safe operating procedure you need, we will get one of our senior safety advisors to write one for you!
These can all be downloaded and are not blank templates, so can be used immediately.
We also provide Induction training to help you on-board new employees and contractors.
As you can see it is all done for you so it makes it nice and simple. You can find out more on the Industries and Professions page.
If you’re concerned about the time commitment and knowledge required to implement the correct documents, procedures and training for your business, Safe-R Outcomes can help. We strive to reduce the time and cost for businesses to implement their legally necessary safety requirements.
In conclusion
Safe operating procedures are an important part of any business or organisation. They provide clear instructions on how to safely carry out tasks or activities and help to prevent accidents and injuries from occurring.
If you haven’t already got one, now is the time to develop a safe operating procedure for your business. And if you have got one, make sure that everyone who needs to use it is properly trained and competent in doing so.