Safe Work Method Statements (SWMS) are critical documents designed to ensure the safety of workers, particularly in high-risk industries such as construction, manufacturing, and mining. A well-crafted SWMS outlines the tasks involved in a job, identifies potential hazards, and details the controls you need. Discover safe work method statement mistakes you might be making and learn practical tips on how to avoid them, ensuring that these vital documents fulfil their purpose of protecting workers and maintaining compliance with safety regulations.
1. Safe Work Method Statement Mistakes: Misidentifying Hazards
Mistake: One of the most critical errors in creating a SWMS is the misidentification of hazards. This can occur when the process of identifying potential risks is rushed or not thorough enough, leading to the omission of significant dangers. Misidentified hazards leave gaps in safety protocols, increasing the likelihood of accidents and injuries.
How to Avoid: Conducting a comprehensive risk assessment is essential before drafting the SWMS. This process should involve a detailed examination of all tasks, work environments, and equipment to identify any possible hazards. It is also crucial to involve the workers who will be performing these tasks, as they can provide valuable insights based on their experience and knowledge of the job. Regularly reviewing and updating hazard identification is necessary as work conditions evolve, ensuring that all potential risks are accounted for and managed.
2. Safe Work Method Statement Mistakes: Failing to Update SWMS Regularly
Mistake: A common mistake is assuming that once a SWMS is created, it does not need further attention. However, work environments, tasks, and safety standards are constantly changing. Failing to regularly update the SWMS to reflect these changes can result in outdated safety measures that no longer address current risks, rendering the SWMS ineffective.
How to Avoid: Implement a systematic approach to reviewing and updating the SWMS regularly. Set specific intervals, such as quarterly, for these reviews, and always reassess the SWMS following any significant changes in work practices, personnel, or equipment. Assign a dedicated safety officer or team to oversee these updates, ensuring that the SWMS remains relevant and effective at all times.
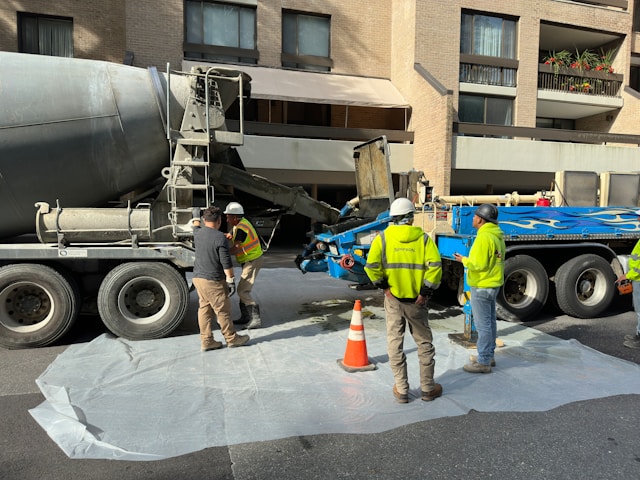
3. Safe Work Method Statement Mistakes: Overlooking Worker Training
Mistake: Even the most meticulously prepared SWMS is ineffective if workers are not adequately trained on its content. This is a significant oversight that can lead to non-compliance and increased risks. Without proper training, workers may not understand the procedures outlined in the SWMS, which can result in unsafe practices.
How to Avoid: Establish a comprehensive training program that covers all aspects of the SWMS. Training should not only focus on what the SWMS contains but also explain why each element is important for worker safety. This training should be mandatory for all workers before they begin their tasks and should be reinforced with regular refresher sessions. Additionally, ensure that the training is tailored to the specific needs and language proficiency of the workforce to maximise understanding and compliance.
4. Safe Work Method Statement Mistakes: Not Including All Necessary Workers
Mistake: Sometimes, SWMS are created with a narrow focus that includes only the most obvious workers directly involved in the tasks. This approach can overlook other personnel who might be indirectly affected by the work, such as subcontractors, temporary workers, or even site visitors. This exclusion can lead to gaps in communication and safety practices, putting these individuals at risk.
How to Avoid: When developing the SWMS, it’s crucial to consider all workers who will be present on-site, including those who might not be directly involved in the task but are still exposed to the associated risks. This includes subcontractors, temporary workers, and any other personnel who might be affected by the work being performed. Ensure that the SWMS is communicated to everyone involved, and that each person understands their role in maintaining safety. Holding regular safety meetings that include all workers can help reinforce this understanding and promote a culture of safety across the entire site.
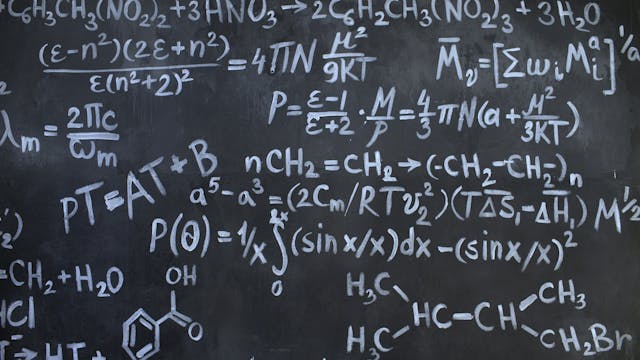
5. Safe Work Method Statement Mistakes: Overcomplicating the SWMS
Mistake: In an effort to cover all bases, some SWMS end up being overly complex, filled with excessive details and technical jargon. While it’s important to be thorough, an overly complicated SWMS can be difficult for workers to understand and follow. This complexity can lead to confusion, misinterpretation, and ultimately, non-compliance with safety procedures.
How to Avoid: The key to an effective SWMS is clarity and simplicity. Write the SWMS in plain language that is easy to understand for all workers, regardless of their level of education or experience. Focus on the essential tasks, hazards, and control measures, and avoid unnecessary jargon or overly technical details. The SWMS should be a practical guide that workers can easily refer to and apply in their day-to-day tasks. Consider using bullet points, flowcharts, or diagrams to convey information clearly and concisely.
6. Safe Work Method Statement Mistakes: Neglecting to Involve Workers in the SWMS Creation
Mistake: Developing a SWMS in isolation, without input from the workers who will actually be performing the tasks, can result in a document that is out of touch with the practical realities of the job. Workers might find that the procedures outlined in the SWMS are unrealistic or difficult to implement, leading to non-compliance and increased risks.
How to Avoid: Involving workers in the SWMS development process is essential for creating a document that is both practical and effective. Workers have firsthand experience with the tasks and can provide valuable insights into potential hazards and effective control measures. By involving them in the creation of the SWMS, you also foster a sense of ownership and commitment to following the procedures outlined in the document. This collaboration can lead to a more accurate and realistic SWMS that workers are more likely to adhere to.
7. Safe Work Method Statement Mistakes: Ignoring Legal and Compliance Requirements
Mistake: Failing to ensure that the SWMS aligns with relevant regulatory requirements is a significant oversight that can lead to serious consequences. Non-compliance with safety regulations can result in fines, penalties, and even legal action, in addition to compromising worker safety.
How to Avoid: Stay informed about the latest workplace health and safety regulations that apply to your industry. Ensure that the SWMS complies with all relevant laws, standards, and guidelines. Regularly consult with legal or safety experts to verify that your SWMS is up to date with current regulations. Additionally, ensure that all workers are aware of the legal requirements and understand their responsibilities in adhering to the SWMS.
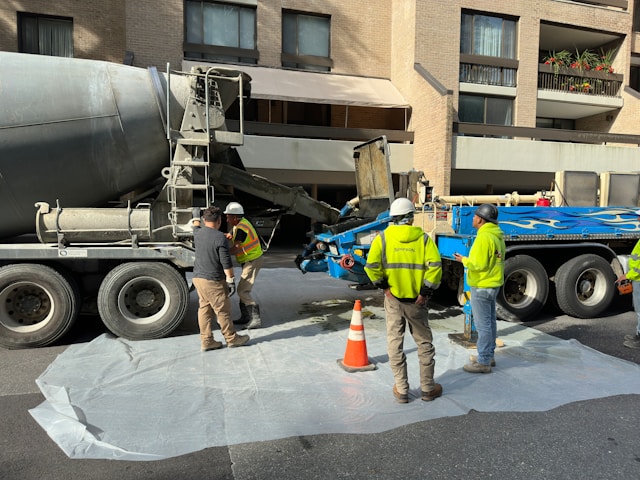
8. Safe Work Method Statement Mistakes: Skipping the Review and Approval Process
Mistake: Rushing the creation of a SWMS without a formal review and approval process can lead to a document that is incomplete or incorrect. Without proper oversight, critical safety elements might be missed, resulting in a SWMS that does not effectively manage risks.
How to Avoid: Establish a clear and structured review and approval process for the SWMS. This should include input from various stakeholders, such as safety officers, supervisors, and other relevant personnel who can provide different perspectives on the potential risks and control measures. The SWMS should only be implemented after it has been thoroughly reviewed and approved by all necessary parties. This process ensures that the SWMS is accurate, comprehensive, and tailored to the specific risks of the job.
9. Safe Work Method Statement Mistakes: Failing to Monitor and Enforce Compliance
Mistake: Even the best SWMS is useless if it is not actively monitored and enforced on the job site. Workers might revert to unsafe practices if compliance is not consistently monitored, leading to increased risks and potential accidents.
How to Avoid: Regular monitoring of compliance with the SWMS is essential to ensure that safety procedures are being followed correctly. This can include spot checks, audits, and feedback sessions with workers. Supervisors should be trained to recognize and address non-compliance issues immediately. Encouraging a culture of safety, where workers feel responsible for not only their own safety but also the safety of their colleagues, can help maintain high compliance levels. Rewarding safe behaviour and promptly addressing non-compliance will reinforce the importance of adhering to the SWMS.
10. Safe Work Method Statement Mistakes: Not Documenting Changes and Incidents
Mistake: When changes to the work environment occur, or when incidents happen, failing to document these in the SWMS can lead to a lack of accountability and the potential for repeat mistakes. Without proper documentation, valuable lessons might be lost, and the SWMS may not reflect the current risks.
How to Avoid: Implement a system for documenting any changes to the SWMS or any incidents that occur on the job site. This documentation should be reviewed and used to update the SWMS as necessary, ensuring that it remains relevant and effective. It’s also important to communicate these changes to all affected workers promptly, so they are aware of any new risks or procedures. Keeping a record of incidents and changes can help identify patterns or recurring issues that need to be addressed to improve overall safety.

Conclusion
Safe Work Method Statements are indispensable tools in ensuring workplace safety, but their effectiveness hinges on proper development, implementation, and maintenance. By avoiding these common safe work method statement mistakes—such as misidentifying hazards, failing to update the SWMS, and overlooking worker training—you can significantly enhance the safety of your workplace and ensure compliance with legal requirements. Regular reviews, worker involvement, and diligent monitoring are key to maintaining a SWMS that truly protects workers and minimises risks. A proactive approach to managing SWMS not only safeguards your team but also fosters a culture of safety that can lead to greater productivity and a more positive work environment.
How can Safe-R Outcomes help your business?
Our Professional subscriptions contain many essential documents including:
- WHS Management Plans / Safety Manuals
- SWMS (if the job entails high risk tasks)
- a range of SOPs, Registers, Toolbox Talks, Checklists and Policies
These can all be downloaded and are not blank templates, so can be used immediately.
We also provide Induction training to help you on-board new employees and contractors.
As you can see it is all done for you so it makes it nice and simple. You can find out more on the Industries and Professions page.
If you’re concerned about the time commitment and knowledge required to implement the correct documents, procedures and training for forklift safety, Safe-R Outcomes can help. We strive to reduce the time and cost for businesses to implement their legally necessary safety requirements.